The following information is provided for reference purposes only and should be used at your own risk
In no event shall Beisan Systems, LLC or its members be liable for incidental, consequential, or special loss or damages of any kind however caused.
Introduction
“Vanos” is BMW’s name for its variable valve timing units. Vanos units take on various shapes and design according to car year and model (engine model). The vanos units discussed here are BMW part # 11-36-7-831-486 and 11-36-7-831-487. They are a double vanos, meaning both the intake and exhaust valve timing is varied. These vanos units are identical with only the solenoid pack and solenoid cover installed upside-down. They are part of BMW 8-cylinder engine S62. This engine is incorporated into the E39 M5 98-03, E52 Z8 Roadster 99-03.
This vanos piston seals and static seal O-rings are made of the correct materials and don’t experience premature failure. However over time and use the piston seal O-rings will experience notable compression set (flattening) and the Teflon rings will experience wear (loss of material). This can lead to degradation in performance. The static seal O-rings will also experience notable compression set and could eventually leak. Thus there is a need for a replacement seals solution for this vanos.
A vanos seals/O-rings repair kit can be acquired through Beisan Systems (bee-saan), www.beisansystems.com/products. It includes a vanos replacement set of OEM equivalent material Teflon rings and Viton O-rings.
Symptoms
Loss of low end torque, uneven power delivery, and overall loss of power.
Diagnosis
The BMW DIS vanos diagnostic test can be run to assess speed and preciseness of adjustment.
Repair Procedure
The following is an E39 M5 vanos seals R&R (remove and replace) procedure.
Repair time: 12 hours mechanic, 12+ hours DIY.
Parts, Tools, and Shop Supplies
Parts with part number pattern xx-xx-x-xxx-xxx are BMW parts and can be acquired from a BMW dealership.
Beisan Systems only provides the seals repair kit.
S62 vanos seals repair kit, MY 98 (BS061.1), MY 99+ (BS061.2) $120/each. Picture is BS061.2.
Note: Car model year 98 utilizes part BS061.1. Subsequent car model years 99+ utilize part BS061.2. The difference between the two products is the piston small seal size.
Note: Seals repair kit covers both vanos units and thus only one seals kit is necessary.
Note: Seals kit incorporates 2 vanos oil pressure restrictor O-rings and 2 secondary air pipe end O-rings
Bank 1 valve cover gasket set (11-12-0-001-269) $62.74/each, bank 2 valve cover gasket set (11-12-0-001-278) $62.74/each
6 x valve cover front bolt grommet (11-12-1-721-879) $1.13/each, 20 x valve cover side bolt grommet (11-12-1-437-395) $1.17/each
2 x coil cover gasket (11-12-1-406-744) $13.25/each
Intake manifold cover gasket (11-61-1-406-657) $36.58, 4 x intake manifold cover O-ring (11-61-1-406-747) $2.12
8 x large vanos solenoid O-ring (11-36-7-830-828) $5.58/each, 8 x small vanos solenoid O-ring (11-36-7-830-829) $5.10 / each
2 x vanos solenoid cover gasket (11-36-1-406-838) $15.22/each
4 x vanos oil hose washer (07-11-9-963-072) $0.51/each
Coolant drain bolt washer (07-11-9-963-225) $0.09/each
Note: BMW vanos solenoid O-rings have been redesigned to have multiple facets to avoid high oil pressure shredding. These are very special O-rings and are only available from BMW.
4 x vanos supporting M6 long bolts (07-12-9-905-554) $1.50/each
Note: Any 6mm diameter, 1.0mm thread pitch, 50+mm long, bolt will do. Indicated BMW part is S54 vanos solenoid mounting bolt.
2 x putty-knife (small, medium), strait pick tool (small), 90 degree pick tool (small)
pliers (medium), medium nose pliers (small), razor knife (small)
27mm combo wrench, short handle adjustable wrench (27mm / 1+”), 22mm combo wrench, 10mm combo/ratcheting wrench, 7mm combo wrench
Flathead screwdriver (small, medium, short), Phillips screwdriver, tack lifter, T25 torx bit driver, tack lifter, magnet pickup, mirror (medium)
32mm socket 1/2″, 19mm socket 1/2″, 19mm deep socket 3/8″, 14mm socket 3/8″, 13mm socket 3/8″, 10mm socket 3/8″, 10mm deep socket 3/8″
10mm socket 1/4″, 6mm socket 1/4″, 5mm socket 1/4″, 6mm hex bit socket 3/8″, 5mm hex bit socket 3/8″
1/2″ ratchet, 1/2″ long-arm ratchet, 3/8″ ratchet, 3/8″ medium-arm ratchet, 3/8″ long-arm ratchet, 1/4″ medium-arm ratchet, 1/4″ long-arm small head ratchet
1/2″ socket extension (short), 3/8″ socket extension (short), 1/4″ socket extension (short, medium wobble, long wobble)
3/8″ torque wrench (8 Nm [6 ft-lb], 14 Nm [10 ft-lb])
V8 mechanical fan removal tools
32mm combo wrench, BMW water pump pulley holder (11-5-050) $20/each
Handheld sledge hammer (3lb)
A Baum Tools water pump pulley holder or holder and 32mm wrench combo can be purchased from El Paso Tool store.
Go to El Paso Tool store and perform a “Store search” for “115050”. Check the “in titles & description” check box.
El Paso Tool store
Paper towels, water based cleaner (simple green 1:10), brake cleaner, spray lubricant
Parts plate, gasket sealant, assembly oil (lubricant oil)
Coolant receptacle (not shown)
1 gallon BMW coolant, 1 gallon distilled water, 1 empty gallon container for mixing (old BMW coolant container)
Repair
Car engine must be cold to perform repair procedure.
Right and Left designations are from car front at hood orientation.
Engine bank 1 head is on left and engine bank 2 head is on right.
Cylinders 1-4 are on bank 1 front to rear, and cylinders 5-8 are on bank 2 front to rear.
Removal of engine air intake
Removal of fan & shroud
Removal of cabin filter housing
E39 cabin filter housing removal
Removal of intake manifold
Remove intake manifold top cover 15 mounting caps; 4 top and 11 perimeter (10mm socket 3/8″ / 3/8″ ratchet & extension).
Pull up and remove intake manifold cover from engine bay.
Remove air intake funnels inside intake manifold.
For each funnel, remove two mounting nuts and remove funnel (10mm socket 3/8″ / 3/8″ medium-length ratchet & extension, magnet pickup).
Note: Cyl 1 & 5 are unique, and cyl 2-4 & 6-8 are same.
Remove intake manifold 33 mounting bolts (10mm socket 3/8″ / 3/8″ ratchet & extension).
Note: Bolts are similar, but slightly longer, than coil ground bolts removed in coming steps. Maintain bolt separation to prevent misuse.
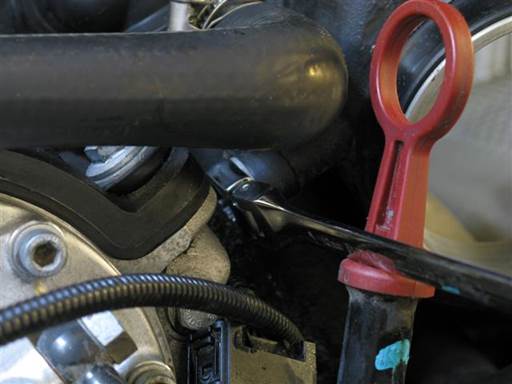
Remove bank 1 & 2 oil separator mounting bolts at front right and left of intake manifold (10mm ratcheting wrench).
Remove intake manifold idle control valve hose at front center of intake manifold.
Loosen hose mounting clamp (6mm socket 1/4″ / 1/4″ ratchet & extension).
Pull hose from intake manifold pipe.
Remove intake manifold oil drain hose at front center of intake manifold.
Loosen hose mounting clamp (5mm socket 1/4″ / 1/4″ ratchet & extension).
Pull hose from intake manifold pipe.
Disconnect bank 1 & 2 oil separators from intake manifold front.
Lift manifold up and to rear and pull out each oil separator neck grommet from manifold.
Lift up and remove intake manifold from engine bay.
Note: Maintain intake manifold gaskets at throttles.
Removal of valve covers
Open trunk and lift up floor cover to access battery.
Open battery cover negative terminal access cover.
Loosen battery negative cable mounting nut (10 mm socket 3/8″ / 3/8″ ratchet & extension).
Remove negative cable clamp from battery negative post and lift above battery cover.
Close negative terminal access cover.
Caution: Do not fully close trunk lid. It cannot be opened using electronic latch. If trunk lid closed, key is needed to mechanically open trunk lid.
Note: Battery negative cable removal is necessary for removal of battery positive cable at engine bank 2 valve cover in coming step.
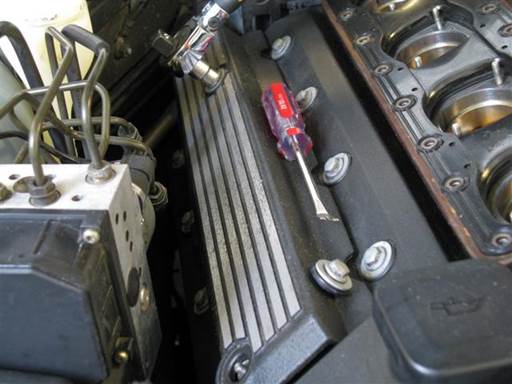
Remove bank 1 & 2 ignition coil cover. For each cover perform following.
Remove 2 cover mounting bolts w/ washers & grommets (10mm socket 3/8″ / 3/8″ ratchet, tack lifter).
Remove coil cover.
Remove coil cover gasket from valve cover.
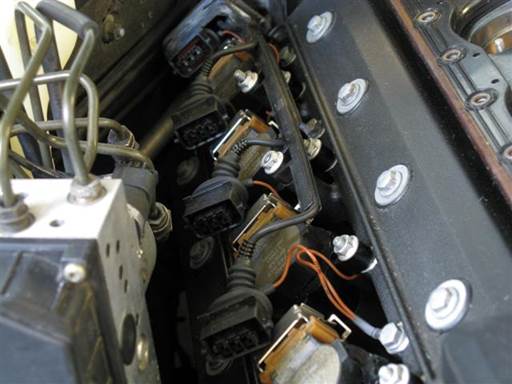
Disconnect bank 1 & 2 ignition coils electrical cable connectors. For each set of coils perform following.
For each coil, pull up on coil connector metal lock and pull off cable electrical connector.
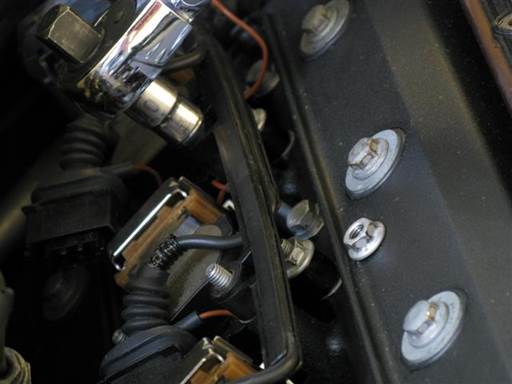
Remove bank 1 & 2 coil harness rail. For each coil harness rail perform following.
Remove coil harness rail mounting nut at front mounting stud (10mm socket 3/8″ / 3/8″ ratchet).
Pull off coil harness rail from mounting studs and set to side.
Note: Rail rear mounting stud does not have mounting nut and is used to mount previously removed coil cover.
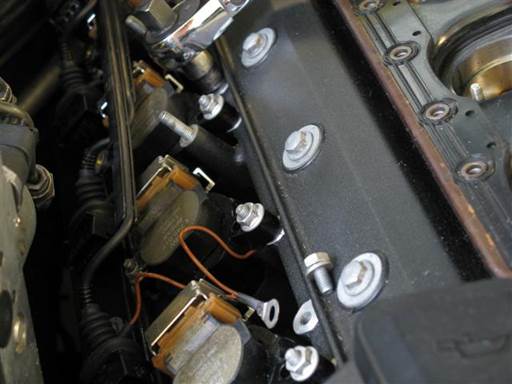
Disconnect bank 1 & 2 coil harness ground wires from valve cover. For each coil harness perform following.
Remove coil harness ground wire mounting bolt at top middle front and rear of valve cover (10mm socket 3/8″ / 3/8″ ratchet).
Note: Bolts are similar, but slightly shorter, than intake manifold mounting bolts removed in previous step. Maintain bolt separation to prevent misuse.
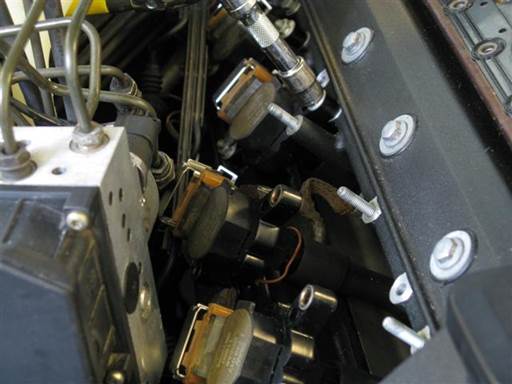
Remove bank 1 & 2 ignition coils. For each set of coils perform following.
Remove 2 mounting nuts at each coil (10mm socket 3/8″ / 3/8″ ratchet & extension).
Pull up and remove all coils.
Note: Maintain coil/cylinder association for reinstallation. This is not necessary, but is good practice.
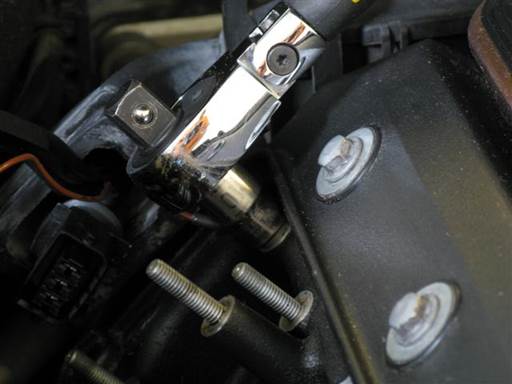
Disconnect bank 1 & 2 coil harness ground wire at top rear of valve cover. For each coil harness perform following.
Remove coil harness ground wire mounting bolt at top rear of valve cover (10mm socket 3/8″ / 3/8″ ratchet).
Note: Bolts are similar, but slightly shorter, than intake manifold mounting bolts removed in previous step. Maintain bolt separation to prevent misuse.
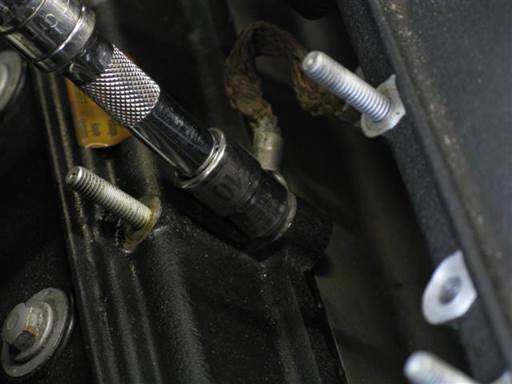
Disconnect bank 1 & 2 valve cover ground strap. For each valve cover ground strap perform following.
Remove valve cover ground strap mounting bolt at valve cover coil well (10mm socket 3/8″ / 3/8″ ratchet & extension).
Note: Bolts are similar, but slightly shorter, than intake manifold mounting bolts removed in previous step. Maintain bolt separation to prevent misuse.
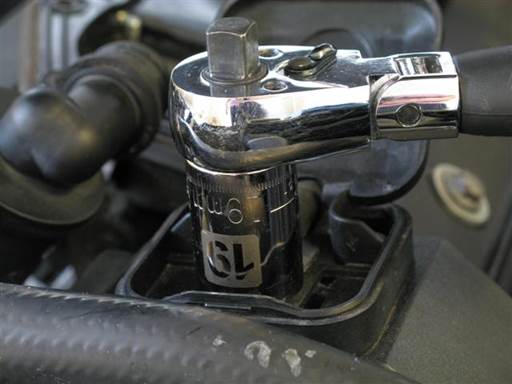
Caution: Battery negative cable must first be disconnected from battery in trunk. This was first step in valve cover removal section.
Remove battery positive cable mounting nut at bank 2 valve cover cable box (19mm socket 1/2″ / 1/2″ ratchet).
Remove battery positive cable from cable box and valve cover and set to side.
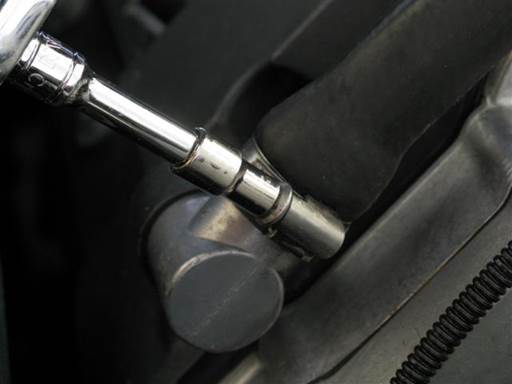
Remove bank 1 & 2 crankcase ventilation hose from valve cover. For each valve cover ventilation hose perform following.
Loosen vent hose mounting clamp at valve cover (6mm socket 1/4″ / 1/4″ ratchet & extension).
Pull hose from valve cover vent pipe.
Remove engine oil filter canister 2 mounting nuts (10mm socket 3/8″ / 3/8″ ratchet & extension).
Lift up engine oil filter canister and move slightly to side and place against power steering reservoir canister.
Note: Slight repositioning of oil filter canister allows for easier removal of bank 2 valve cover in coming step.
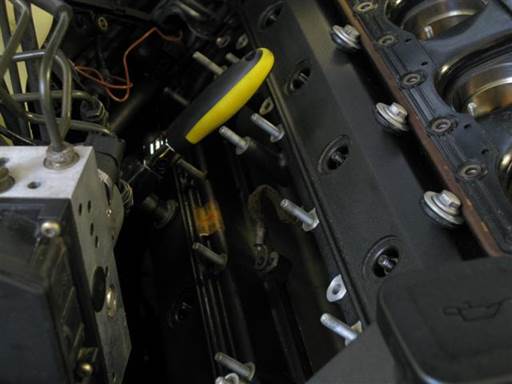
Remove bank 1 & 2 valve cover mounting bolts. For each valve cover perform following.
Remove 11 valve cover mounting bolts w/ washers & grommets; 3 front and 4 at each side (10mm socket 3/8″ / 3/8″ ratchet & extension, tack lifter).
Note: Front 3 bolts are different from 8 side bolts.
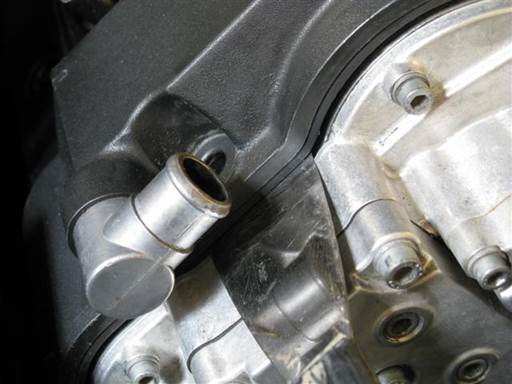
Remove bank 1 & 2 valve cover. For each valve cover perform following.
Insert blade (medium putty-knife) between valve cover gasket and engine head at all front end accessible locations to break gasket bond.
Pull up and remove valve cover. If resistant, insert blade (medium putty-knife) between valve cover gasket and engine head at sticking locations.
Note: If valve cover cannot be removed, double check valve cover 11 mounting bolts have been removed. If valve cover is stuck, pull up on free front end of cover to break gasket bond on remainder of valve cover.
Remove valve cover perimeter gasket.
Remove valve cover sparkplug well gasket.
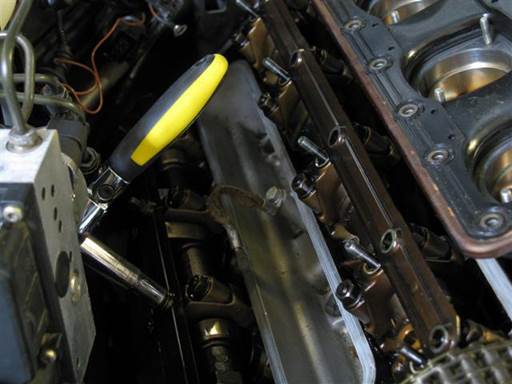
Remove bank 1 & 2 camshaft oil rails. For each set of oil rails perform following.
Remove intake and exhaust oil rail 5 mounting nuts (10mm deep socket 3/8″ / 3/8″ ratchet, 10mm ratcheting wrench).
Remove oil rails.
Note: Bank 1 & 2 oil rails are different lengths.
Note: Oil rails are symmetrical front to rear and top to bottom. Thus maintaining oil rail orientation is not necessary.
Draining of coolant
Raise front of car and place on jack stands (follow appropriate procedure; chock both sides of both rear wheels).
Remove large engine compartment shield underneath front of car.
Note: To remove engine compartment shield, transmission shield to rear of it has to be removed first.
Remove transmission shield. Loosen transmission shield perimeter mounting bolts 1/2 turn to release lock (Phillips). Remove transmission shield.
Loosen engine compartment shield perimeter mounting bolts 1/2 turn to release lock (Phillips).
Pull engine compartment shield out from front bumper and remove.
Drain coolant from engine block.
Remove engine left side (front orientation) coolant drain bolt (13mm socket 3/8″ / 3/8″ ratchet).
Note: Drain bolt is located on engine block between cyl 2 & 3.
Catch draining coolant in receptacle (coolant receptacle).
Lift up coolant expansion tank to drain coolant from it.
Remove and discard drain bolt crush washer.
Note: If washer not on bolt it is likely at hole or fallen in coolant receptacle.
Note: It is not necessary to drain coolant from engine right side. This does not affect repair and there is very little coolant to drain and thus is of no significance.
Drain coolant form radiator drain hole.
Turn radiator drain plug at bottom of radiator 1/4 turn and pull off from radiator (pliers).
Catch draining coolant in receptacle (coolant receptacle).
Install engine left side coolant drain bolt.
Install new crush washer on drain bolt.
Install drain bolt (13mm socket 3/8″ / 3/8″ ratchet).
Fully tighten, 25 Nm (18.5 ft-lb) (by feel) (13mm socket 3/8″ / 3/8″ ratchet).
Install radiator drain plug.
Insert drain plug into radiator drain hole and turn 1/4 turn (pliers).
Install large engine compartment shield underneath front of car.
Insert shield front inside front bumper.
Align and insert perimeter bolts into bolt holes.
Turn perimeter mounting bolts 1/2 turn clockwise to install (Philips).
Install transmission shield. Mount shield in position. Align and insert perimeter bolts into bolt holes. Turn perimeter mounting bolts 1/2 turn clockwise to install (Philips).
Lower car from jack stands (follow appropriate procedure).
Removal of coolant hoses
Remove radiator upper hose from radiator.
Pull out hose locking wire clip (small flathead).
Wiggle and pull hose connector off radiator.
Remove radiator lower hose from radiator.
Remove temperature sensor cable connector. Press in connector locking wire clip and pull off connector.
Pull out hose locking wire clip (small flathead).
Wiggle and pull hose connector off radiator.
Remove upper radiator hose from thermostat housing
Loosen hose mounting clamp (6mm socket 1/4″ / 1/4″ ratchet & extension).
Pull hose from thermostat and remove hose.
Remove lower radiator hose from thermostat housing
Loosen hose mounting clamp (6mm socket 1/4″ / 1/4″ ratchet & extension).
Pull hose from thermostat and remove hose.
Remove coolant expansion tank hose form thermostat housing.
Loosen hose mounting clamp (6mm socket 1/4″ / 1/4″ ratchet & extension).
Pull hose from thermostat housing pipe.
Remove coolant expansion tank cable electrical connector.
Press in connector clip and pull off connector.
Remove expansion tank with hose from engine bay.
Setting of engine timing to TDC
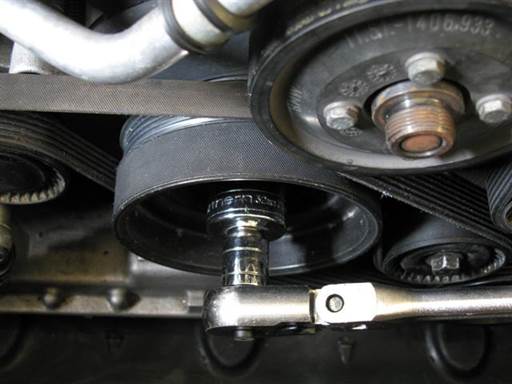
If manual transmission, place transmission in neutral. This allows turning of crankshaft.
Turn crankshaft pulley clockwise until cylinder 1 (bank 1) intake and exhaust cams point to each other at ~45 degree angle (32mm socket 1/2″ / 1/2″ long-arm ratchet & short extension).
Note: Turning crankshaft counter clockwise is acceptable.
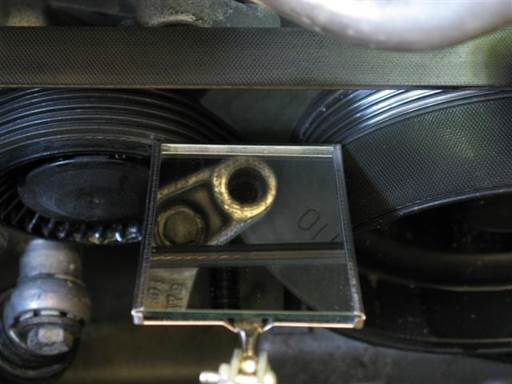
Inspect TDC (top dead center) timing marks on engine timing cover and crankshaft harmonic balancer at ~11 o’clock position (mirror).
Adjust crankshaft pulley to align TDC timing marks (32mm socket 1/2″ / 1/2″ long-arm ratchet & short extension).
Note: Timing marks are far from each other and thus difficult to align. It is easier to align locking pin holes in harmonic balancer and locking bracket (picture).
Note: Turning crankshaft counter clockwise is acceptable.
Note: Precise alignment is not necessary.
Removal of vanos solenoids
To position vanos engine timing, it is easiest to remove vanos solenoids to relieve hydraulic control and allow manual (by hand) vanos and camshaft positioning.
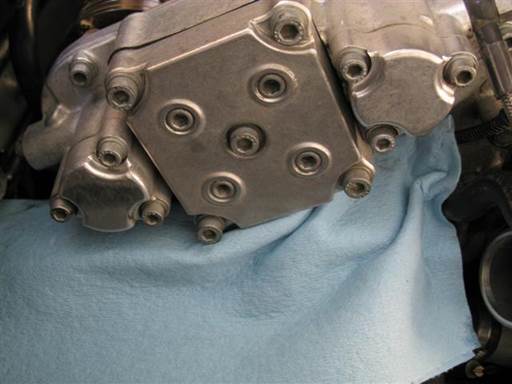
Place towels under bank 1 & 2 vanos. For each vanos perform following.
Fold towels and place under vanos (towels).
Note: Towels will catch draining oil from vanos solenoid housing in coming steps.
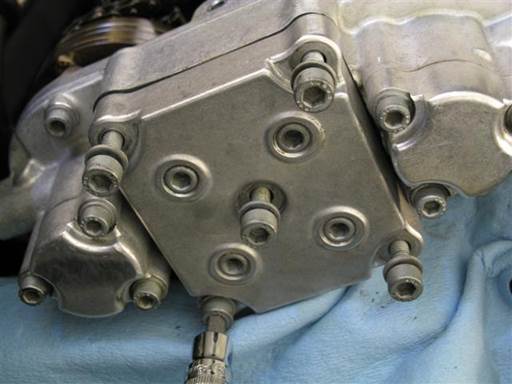
Remove bank 1 & 2 vanos solenoid cover. For each vanos perform following.
Remove vanos solenoid cover 5 mounting bolts (6mm hex bit socket 3/8″ / 3/8″ ratchet).
Remove solenoid cover and cover gasket. Tear cover paper gasket as needed to remove.
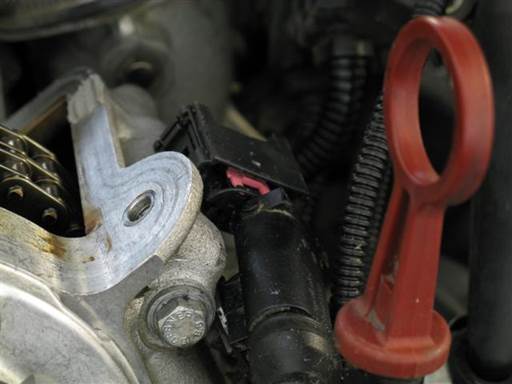
Remove bank 1 & 2 vanos solenoid electrical cable connector. For each vanos perform following.
Slide solenoid cable connector off mounting clip on engine head.
Note: Solenoid cable mounting clip is brittle and easily breaks.
Press in cable connector side clips and wiggle connector off.
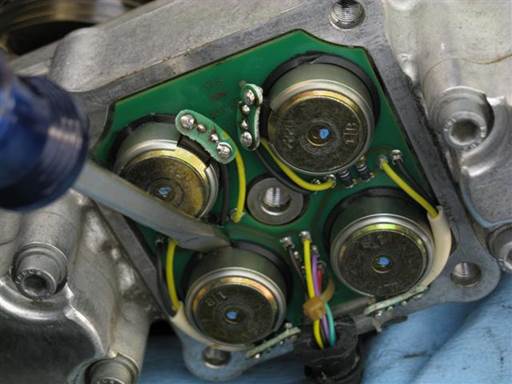
Dislodge bank 1 & 2 vanos two lower solenoids from vanos housing. For each vanos perform following.
Pry out vanos two lower solenoids by prying from middle groove and leveraging against upper solenoid to dislodge from solenoid housing (flathead).
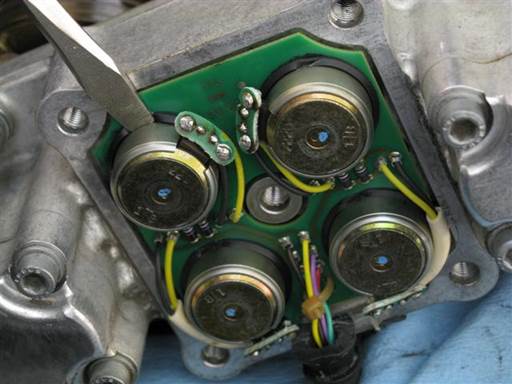
Dislodge bank 1 & 2 vanos two upper solenoids from vanos housing. For each vanos perform following.
Pry out vanos two upper solenoids by prying from middle groove and leveraging against vanos body to dislodge from solenoid housing (flathead).
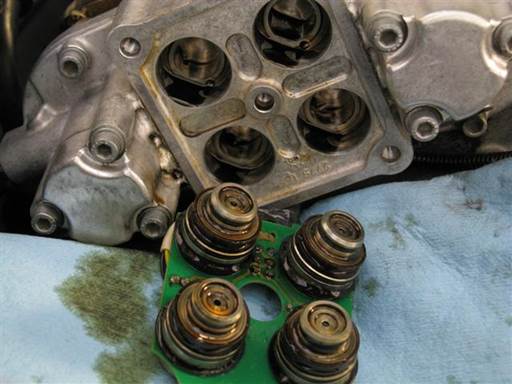
Remove bank 1 & 2 solenoids from vanos. For each vanos perform following.
Remove solenoids with PC board and electrical cable from vanos.
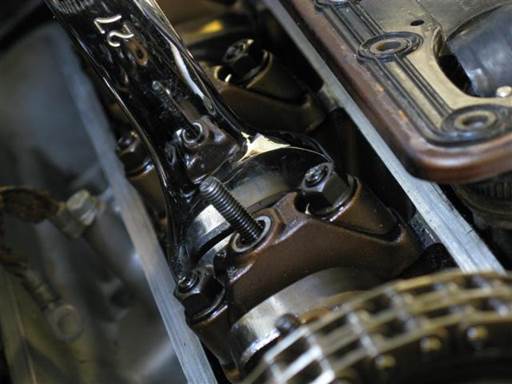
Fully retard banks 1 & 2 intake camshaft timing. For each intake camshaft perform following.
Place open wrench (27mm open wrench) on intake camshaft hex at front of camshaft.
Rotate intake camshaft counter clockwise to adjustment end position. If camshaft resistant to rotation rock camshaft back and forth to release seize.
Note: Camshaft rotation is most effective when standing at side of car.
Note: Splined shaft can be seen protruding from sprocket hub front when camshaft is at adjustment end position.
Note: Camshaft adjustment causes full camshaft timing retard. This causes splined shaft and vanos piston forward positioning. This facilitates access for disconnecting splined shaft from vanos piston in coming step.
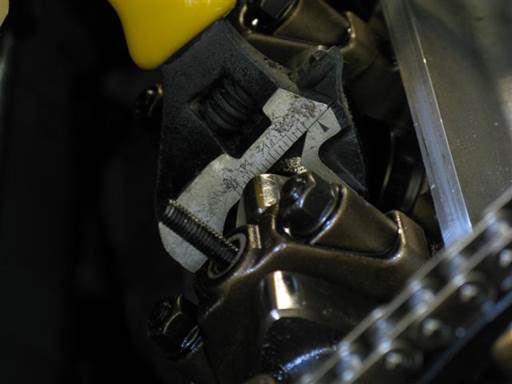
Fully retard banks 1 & 2 exhaust camshaft timing. For each exhaust camshaft perform following.
Place open wrench (27mm open wrench, short handle adjustable wrench) on exhaust camshaft hex at front of camshaft.
Note: Access is limited for standard 27mm open wrench. Use short handle adjustable wrench as needed.
Rotate exhaust camshaft counter clockwise to adjustment end position. If camshaft resistant to rotation rock camshaft back and forth to release seize.
Note: Camshaft rotation is most effective when standing at side of car.
Note: Splined shaft can be seen protruding from sprocket hub front when camshaft is at adjustment end position.
Note: Camshaft adjustment causes full camshaft timing retard. This causes splined shaft and vanos piston forward positioning. This facilitates access for disconnecting splined shaft from vanos piston in coming step.
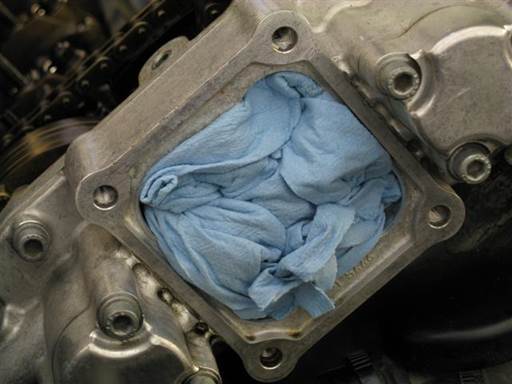
Install towel in bank 1 & 2 vanos solenoid housing. For each vanos perform following.
Remove towels under vanos.
Clean vanos solenoid housing (brake cleaner & towels).
Install towel in vanos solenoid housing and crumple and press towel into each solenoid housing cavity.
Removal of vanos hydraulic attachments
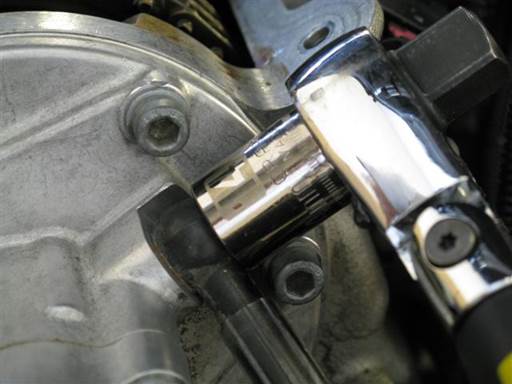
Remove bank 1 & 2 vanos oil accumulator hose. For each vanos perform following.
Remove oil hose mounting banjo bolt at vanos (14mm socket 3/8″ / 3/8″ ratchet).
Discard crush washer at each side of hose fitting.
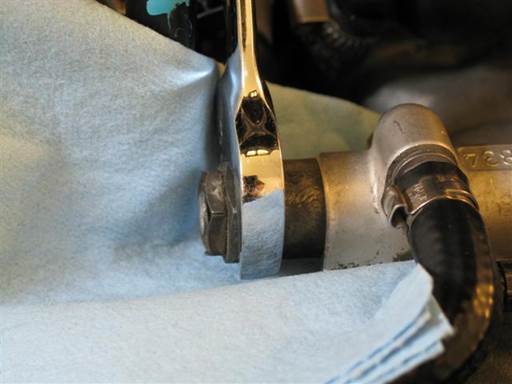
Remove vanos oil pressure restrictor from oil distribution piece (engine front).
Place towel under distribution piece and restrictor to catch draining oil (towels).
Remove oil pressure restrictor (22mm open wrench).
Perform rattle procedure
If performing rattle repair, follow rattle procedure at this time.
S62 Vanos Rattle Procedure
Removal of vanos units from engine heads
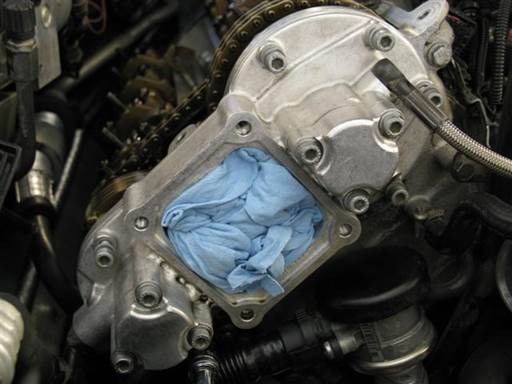
Remove bank 1 & 2 vanos mounting bolts. Perform following for each vanos.
Remove vanos 9 mounting bolts (5mm hex bit socket 3/8″ / 3/8″ ratchet & extension).
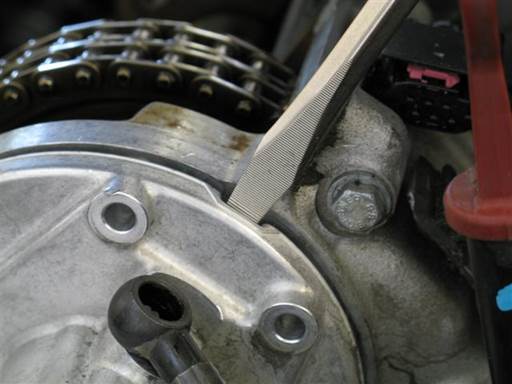
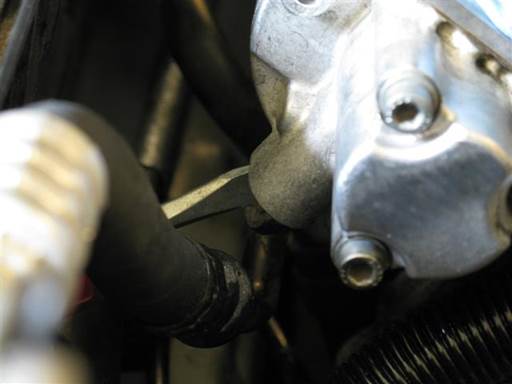
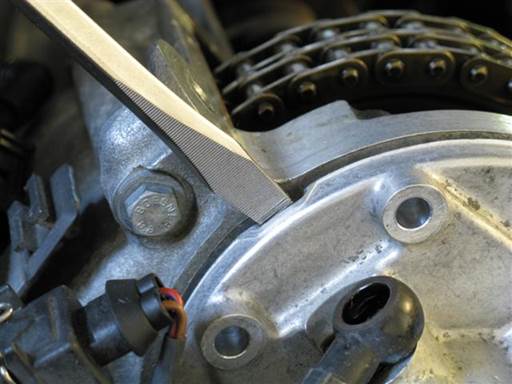
Pry bank 1 & 2 vanos from engine head. Perform following for each vanos.
Pry vanos from engine head at intake and exhaust side designated slots (flathead, short flathead).
Pry vanos evenly until vanos releases from engine head (vanos seal O-rings disconnect from upper timing cover).
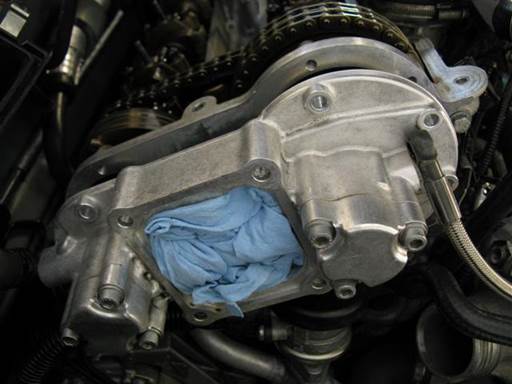
Pull bank 1 & 2 vanos fully forward from engine head.
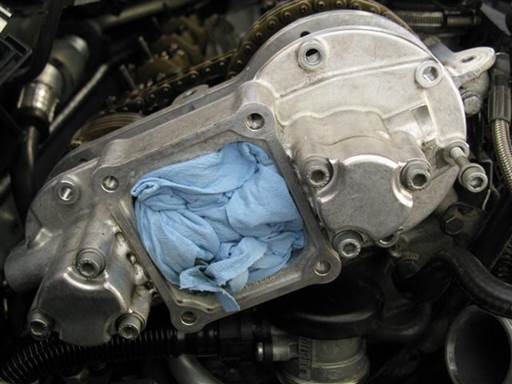
Install long supporting bolt at bank 1 & 2 vanos right and left side.
Install bolts with two rotations.
Note: Vanos supporting bolts support vanos and allow disconnecting vanos intake and exhaust pistons from splined shafts.
Disconnecting of vanos pistons from splined shafts
Perform following procedure of disconnecting vanos intake and exhaust pistons from splined shafts for bank 1 & 2 vanos units.
Note: Bank 2 shown.
Rotate vanos intake piston to allow tool access to splined shaft stud flats (10mm open wrench).
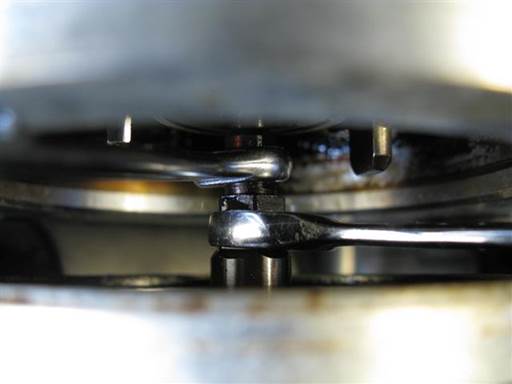
Disconnect vanos intake piston from intake splined shaft stud.
Counter hold splined shaft stud and unscrew vanos piston; left hand thread (7mm open wrench, 10mm open wrench).
Note: Piston and shaft stud are left hand thread, thus unscrew by turning piston tool (10mm open wrench) from left to right (clockwise) (car front orientation).
Rotate vanos exhaust piston to allow tool access to splined shaft stud flats (10mm open wrench).
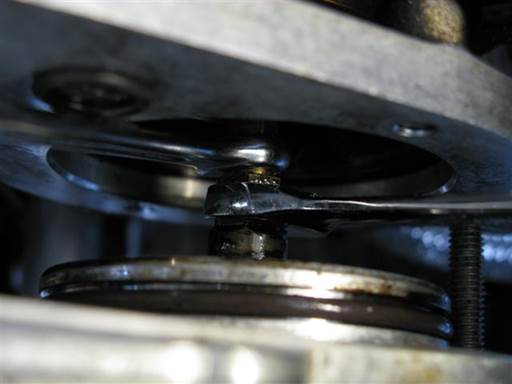
Disconnect vanos exhaust piston from exhaust splined shaft stud.
Counter hold splined shaft stud and unscrew vanos piston; left hand thread (7mm open wrench, 10mm open wrench).
Note: Piston and shaft stud are left hand thread, thus unscrew by turning piston tool (10mm open wrench) from left to right (clockwise) (car front orientation).
Repeat above procedure of disconnecting vanos intake and exhaust pistons from splined shafts for second bank.
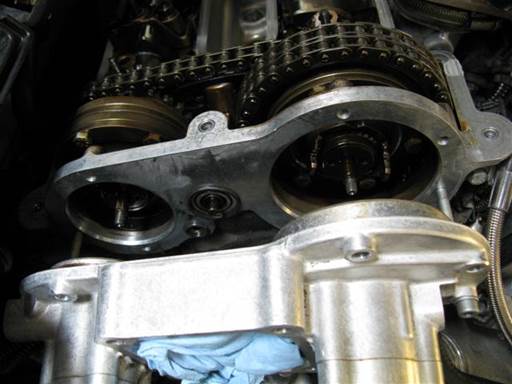
Remove bank 1 & 2 vanos from engine head. Perform following for each vanos.
Pull vanos forward off engine head.
Unscrew vanos right and left side supporting bolts and remove and take vanos to work bench.

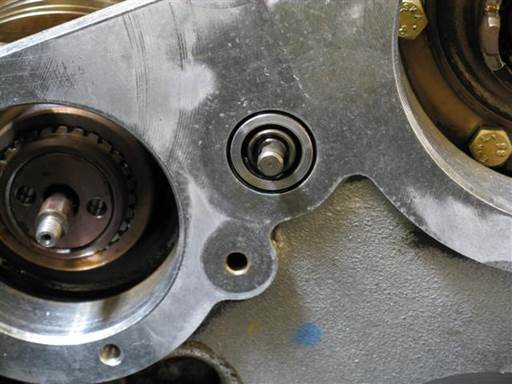
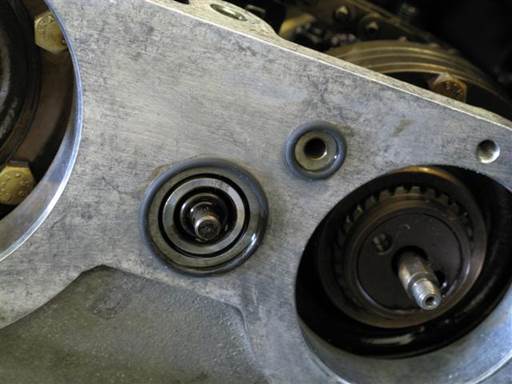
Remove bank 1 & 2 vanos oil input regulator and oil return hole sealing O-rings stuck on upper timing cover.
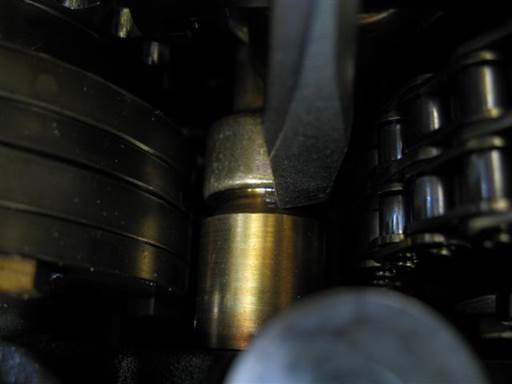
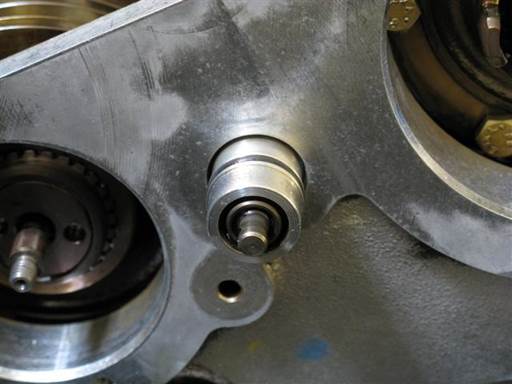
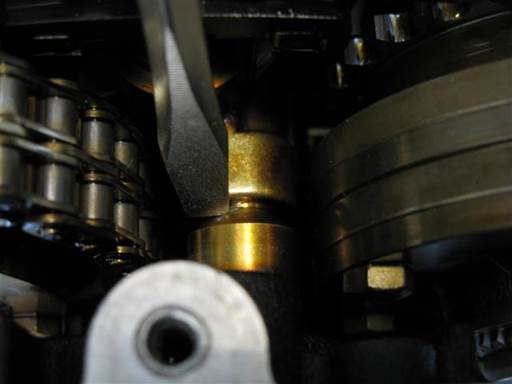
Remove bank 1 & 2 oil input regulator from engine head by prying out regulator at rear (flathead) and pulling out from front.
Installation of vanos seals
During following seals installation procedure, great care should be taken to not drop and damage vanos components. Perform work over table, so if part is dropped it will fall to table top.
Installation of vanos piston seals
Following procedure shows installation of vanos intake piston seals. Same procedure applies to vanos exhaust piston seals.
Remove vanos cylinder cover.
Remove cover 3 mounting bolts (5mm hex bit socket 3/8″ / 3/8″ ratchet).
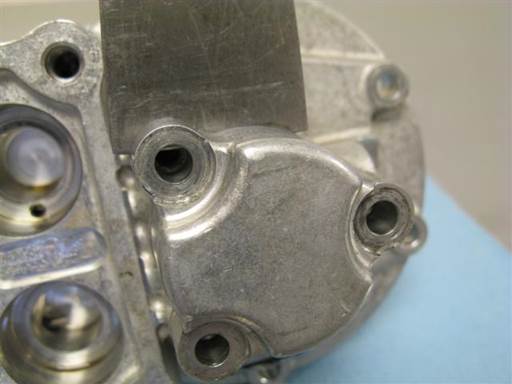
Remove cylinder cover.
Pry cover at multiple locations to evenly remove cover (small putty-knife).
As necessary, strike blade between cover and vanos body to initially break seize.
Note: Orient blade with edge ramp side to vanos body. This orientation is more effective.
Note: Cover resistance is due to cover sealing O-ring.
Remove piston from cylinder.
Press piston from vanos inboard side to remove piston from vanos outboard side (1/4″ socket extension).
Cut cross section of piston middle seal Teflon ring (razor knife).
Note: Rocking of blade while pressing helps create cutting motion.
Rotate blade in seal after cutting to note any remaining uncut seal (razor knife).
Remove cut Teflon ring from piston grove.
Cut cross section of piston middle seal O-ring (razor knife).
Note: Rocking of blade while pressing helps create cutting motion.
Rotate blade in seal after cutting to note any remaining uncut seal (razor knife).
Remove cut O-ring from piston grove.
Cut cross section of piston end seal Teflon ring (razor knife).
Note: Rocking of blade while pressing helps create cutting motion.
Rotate blade in seal after cutting to note any remaining uncut seal (razor knife).
Remove cut Teflon ring from piston grove.
Cut cross section of piston end seal O-ring (razor knife).
Note: Rocking of blade while pressing helps create cutting motion.
Rotate blade in seal after cutting to note any remaining uncut seal (razor knife).
Remove cut O-ring from piston grove.
When seals removal is complete, piston seal grooves will have exposed metal with no seals.
Clean piston (brake cleaner & towels).
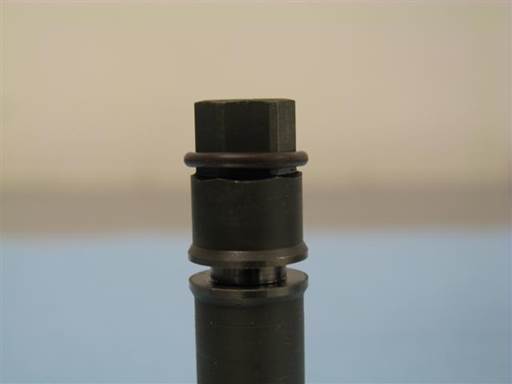
Mount piston middle seal O-ring onto piston small end and roll O-ring along piston and drop into seal groove (fingers).
Center O-ring in seal groove (strait pick).
Mount piston middle seal Teflon ring onto piston small end.
Insert pick tool between Teflon ring and piston (90 degree pick) (picture).
Leverage pick tool against piston and tilt pick tool to stretch out Teflon ring (90 degree pick).
Perform Teflon ring stretching at multiple locations along Teflon ring until Teflon ring notably stretches.
Note: Teflon ring needs to stretch sufficiently to slide over piston larger diameter.
Place piston vertically with large end down.
Press down on Teflon ring from top end to press Teflon ring onto piston larger diameter (fingers/nails).
Move Teflon ring evenly along piston (picture).
Note: If Teflon ring difficult to press down repeat previous Teflon ring stretching step.
Slide Teflon ring down piston to seal groove rim (fingers/nails) (picture).
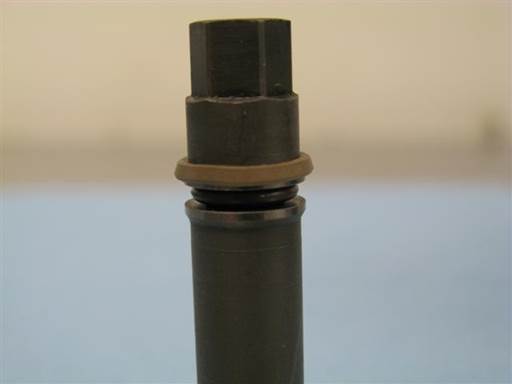
Press down on Teflon ring from top end to press Teflon ring onto piston seal groove rim and drop Teflon ring into seal groove (fingers/nails).
Move Teflon ring evenly along piston (picture).
Note: It has been found that it is practical to first compress this small Teflon ring as next step and insert it into the exhaust cylinder for a few minutes, as shown a few steps below.
After that continue here with the ring on the piston bottom.
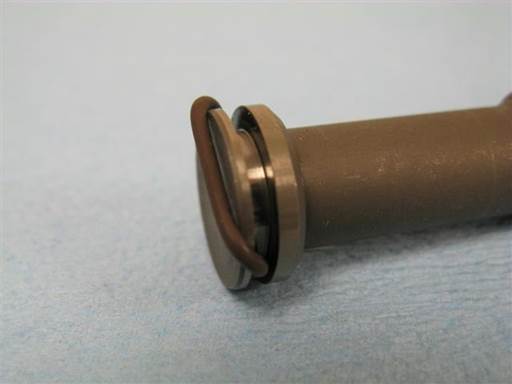
Insert piston end seal O-ring in piston seal groove at one end and stretch other end over piston and drop into seal groove (fingers).
Center O-ring in seal groove (strait pick).
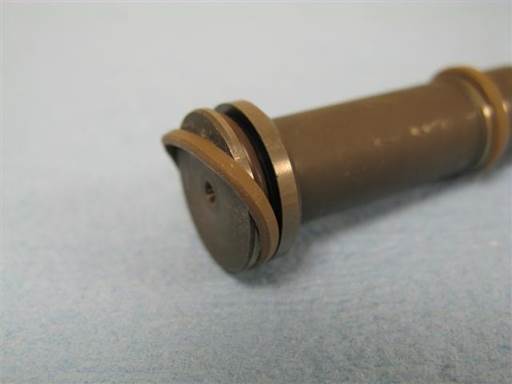
Insert piston end seal Teflon ring in piston seal groove at one end and stretch other end over piston and drop into seal groove (fingers).
Stretch Teflon ring at multiple location along Teflon ring before final stretch over piston and into groove (fingers).
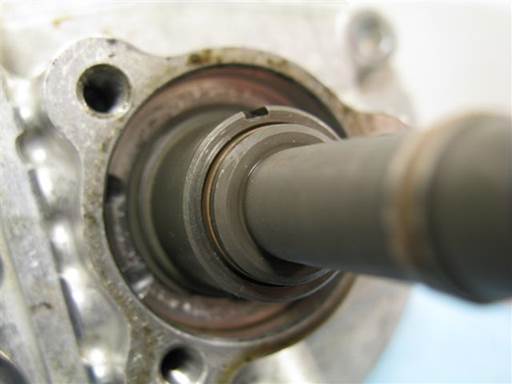
Insert piston large end into cylinder outboard side.
Lightly lubricate cylinder entry inner wall and piston Teflon ring (assembly oil).
Wiggle piston and press strait into cylinder.
Verify Teflon ring is inserting into cylinder at all perimeter locations. Reposition piston and reattempt insertion to facilitate Teflon ring full perimeter insertion.
Once all Teflon ring perimeter inserts into cylinder, wiggle piston and press strait into cylinder to fully insert Teflon ring into cylinder.
Note: Cylinder entry has chamfer which allows for stretched Teflon ring to be collected and inserted into cylinder.
Maintain piston in cylinder for 1 minute then remove.
This period allows Teflon ring to be compressed (resized) close to original size.
Remove piston from cylinder.
Note Teflon ring has decreased in diameter.
Place small hose clamp around piston middle seal Teflon ring (small hose clamp).
Tighten clamp until it seats on piston (Philips).
Note: Only lightly tighten clamp on piston.
Note: Mounting clamp on piston middle seal Teflon ring will compress Teflon ring to close to original size and allow piston insertion in next step.
Remove hose clamp from piston (Philips).
Note Teflon ring has compressed.
Note: Clamp will leave slight crease on Teflon surface. This crease will rectify once Teflon ring is heated in engine.
Lightly lubricate piston middle seal Teflon ring (assembly oil).
Insert piston small end into exhaust cylinder outboard side.
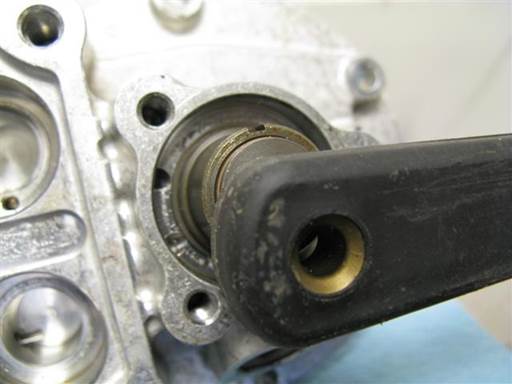
Place flat object on piston end (small putty-knife handle).
Press in on piston with moderate pressure until piston inserts into cylinder (picture).
Note: During this step piston middle seal Teflon ring is being inserted into smaller cylinder. Cylinder entry has chamfer which will allow for stretched Teflon ring to be collected and inserted into cylinder.
Maintain piston in cylinder for 1 minute then remove.
This period allows Teflon ring to be compressed (resized) close to original size.
Remove piston from cylinder by pressing piston from inboard side.
Note Teflon ring has decreased in diameter.
Insert piston small end first into cylinder outboard side and press piston fully into cylinder.
Clean vanos cylinder outboard side cover mating surfaces and cover mounting bolts (brake cleaner & towels).
Remove cylinder cover sealing O-ring.
Pry O-ring from cover groove and remove from cover (90 degree pick).
Clean cylinder cover (brake cleaner & towels).
Install new O-ring on cylinder cover.
Insert O-ring in cover groove on one end and stretch other end over cover and drop into groove (fingers).
Lightly lubricate O-ring to ease cover installation (assembly oil).
Install cylinder cover on vanos.
Orient cover to align cover holes with vanos holes. Cover is asymmetric and only one orientation aligns.
Install cover 3 mounting bolts (5mm hex bit socket 3/8″ / 3/8″ ratchet).
Tighten bolts evenly to draw cover evenly to vanos body.
Fully tighten, 10 Nm (7 ft-lb) (5mm hex bit socket 3/8″ / 3/8″ torque wrench).
Note: Tighten bolts evenly in multiple passes. Verify one pass with all bolts fully tightened.
Repeat above piston seals installation procedure for exhaust side.
Installation of vanos solenoid O-rings
Remove a solenoid small O-ring (90 degree pick).
Remove same solenoid large O-ring (90 degree pick).
Remove remaining solenoid O-rings (90 degree pick).
Install all solenoid new small and large O-rings (fingers).
Install each O-ring over solenoid and roll into groove.
Manipulate O-ring in groove to position correctly.
Note: Solenoid O-rings are special and have many facets. Inspection and repositioning of O-ring is needed for correct installation.
Repeat above solenoid O-rings installation procedure for second vanos solenoid.
Installation of vanos remaining O-rings
Remove vanos inboard intake head sealing O-ring.
Pry O-ring from housing groove and remove from vanos (90 degree pick).
Clean O-ring housing groove (brake cleaner & towels).
Install new O-ring on vanos inboard intake head sealing housing.
Insert new O-ring in housing groove on one end and stretch other end over housing and drop into groove (fingers).
Lightly lubricate O-ring to ease vanos installation (assembly oil).
Remove vanos inboard exhaust head sealing O-ring.
Pry O-ring from housing groove and remove from vanos (90 degree pick).
Clean O-ring housing groove (brake cleaner & towels).
Install new O-ring on vanos inboard exhaust head sealing housing.
Insert new O-ring in housing groove on one end and stretch other end over housing and drop into groove (fingers).
Lightly lubricate O-ring to ease vanos installation (assembly oil).
Install new O-rings on vanos inboard oil drain and oil regulator head sealing faces.
Clean O-ring face grooves (brake cleaner & towels).
Insert new O-ring in face groove (fingers).
Note: Strongly stretch oil regulator O-ring to increase diameter and allow mounting.
Note: Oil drain O-ring is same size as oil pressure regulator small O-ring.
Remove regulator small O-ring.
Pry O-ring from regulator groove and remove from regulator (90 degree pick).
Remove regulator large O-ring.
Pry O-ring from regulator groove and remove from regulator (90 degree pick).
Clean oil flow regulator (brake cleaner & towels).
Install new small O-ring on regulator.
Insert O-ring in regulator groove on one end and stretch other end over regulator and drop into groove (fingers).
Lightly lubricate O-ring to ease vanos installation (assembly oil).
Install new large O-ring on regulator.
Insert O-ring in regulator groove on one end and stretch other end over regulator and drop into groove (fingers).
Lightly lubricate O-ring to ease regulator installation (assembly oil).
Repeat above O-rings installation procedure for second vanos.
Pull off oil filter from pressure restrictor (pliers).
Note: Oil filter replacement is not a requirement. Oil filter can be spray cleaned (brake cleaner).
Cut cross section of small O-ring on pressure restrictor (razor knife).
Note: Rocking of blade while pressing helps create cutting motion.
Note: Take care to not cut or damage adjacent plastic washer. Plastic washer already has cross section cut which is needed for installation.
Remove cut O-ring from pressure restrictor.
Remove large O-ring from pressure restrictor (90 degree pick).
Clean pressure restrictor (brake cleaner & towels).
Install new large O-ring on pressure restrictor. Roll O-ring onto pressure restrictor till O-ring drops into base groove.
Install small O-ring on pressure restrictor. Roll O-ring onto pressure restrictor till O-ring drops into groove.
Install new oil filter on pressure restrictor. Press filter small hole end onto pressure restrictor end stud.
Cleaning of parts
Note: When cleaning parts, spray cleaning compound on towel then wipe component with towel. Components can also be placed in a small container and sprayed with cleaning compound then individually wiped with towel.
Remove and discard valve cover bolt grommets. Cut off valve cover front 3 bolt grommets (diagonal cutters).
Clean all mounting bolts, nuts, washers (brake cleaner & towels).
Clean heads matting surfaces; sparkplug well, valve cover perimeter, timing cover, camshaft bearing cap studs (brake cleaner & towels).
Clean coils ground straps and coil harness ground wire ends (brake cleaner & towels).
Clean coils mounting hole surfaces.
Clean battery positive cable mounting end (brake cleaner & towels).
Remove valve cover gaskets and top cover gaskets from valve covers.
Clean valve cover mating surfaces; inner gasket grooves, bolt access holes, coil mounting studs, ground strap/wire holes, vent pipe, battery cable stud (brake cleaner & towels).
Remove intake manifold cover gasket and 4 cover O-rings at manifold towers.
Clean intake manifold and intake manifold cover mating surfaces, mounting holes and studs, hose pipes (brake cleaner & towels).
Clean throttle intake manifold mounting studs (brake cleaner & towels).
Installation of vanos units on engine heads
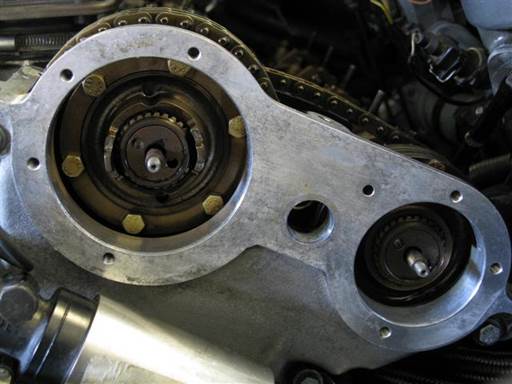
Verify bank 1 & 2 upper timing covers vanos matting surfaces are clean (brake cleaner & towels).
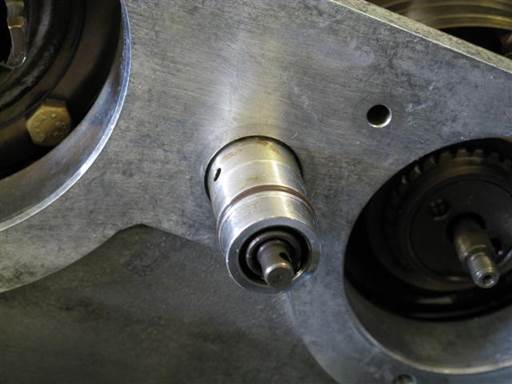
Insert bank 1 & 2 vanos oil input regulator into upper timing cover hole and orient with side oil relief holes to right and left.
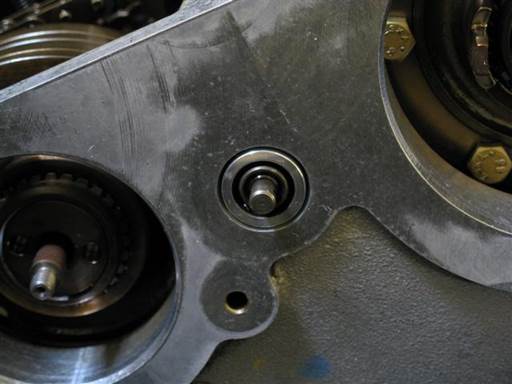
Press bank 1 & 2 vanos oil input regulator into head until flush with upper timing cover face (picture).
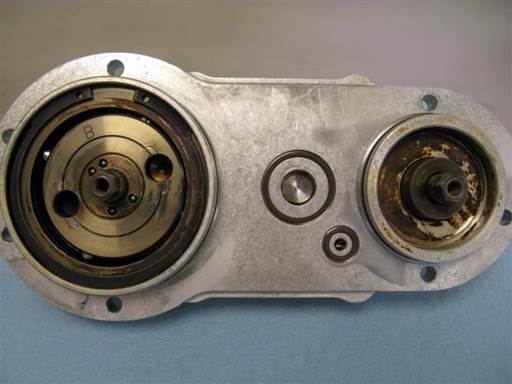
Clean bank 1 & 2 vanos unit head matting surfaces (brake cleaner & towels) and pull pistons fully out of vanos (medium nose pliers).
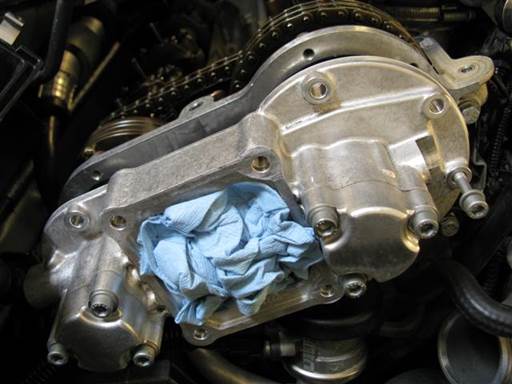
Mount bank 1 & 2 vanos on engine head. Perform following for each vanos.
Note: Vanos units are same and interchangeable, but it’s best practice to maintain vanos to engine head association. Vanos is originally oriented with vanos sticker to bottom.
Mount vanos on engine head with vanos long supporting bolt at right and left side of vanos. Install supporting bolts with 2 turns.
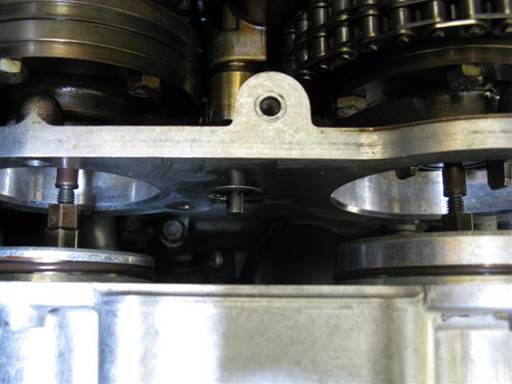
Push bank 1 & 2 vanos units towards engine heads until vanos piston ends touch splined shaft studs.
Connecting of vanos pistons to splined shafts
Perform following procedure of mounting vanos intake and exhaust pistons to splined shafts and inserting vanos onto engine head for bank 1 & 2 vanos units.
Note: Bank 1 shown.
Rotate intake splined shaft stud to facilitate tool access to stud flats (fingers).
Mount splined shaft stud tool (7mm open wrench).
Install pliers on vanos intake piston hex (medium nose pliers).
Lift up vanos and pull vanos intake piston onto splined shaft stud (medium nose pliers).
While pressing piston onto splined shaft, counter hold splined shaft stud and thread piston onto splined shaft stud one rotation; left hand thread (medium nose pliers / 7mm open wrench).
Note: Piston and shaft stud are left hand thread, thus screw by turning piston tool (medium nose pliers) from right to left (counter clockwise) (car front orientation).
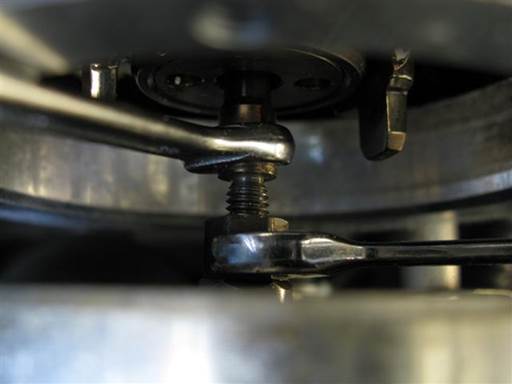
Thread intake piston onto splined shaft stud; left hand thread (10mm open wrench / 7mm open wrench).
Note: Piston and shaft stud are left hand thread, thus screw by turning piston tool (10mm open wrench) from right to left (counter clockwise) (car front orientation).
Moderately tighten; left hand thread (10mm open wrench / 7mm open wrench).
Note: Due to left hand thread, it is not necessary to over tighten joint.
Rotate exhaust splined shaft stud to facilitate tool access to stud flats (fingers).
Mount splined shaft stud tool (7mm open wrench).
Install pliers on vanos exhaust piston (medium nose pliers).
Lift up vanos and pull vanos exhaust piston onto splined shaft stud (medium nose pliers).
While pressing piston onto splined shaft, counter hold splined shaft stud and thread piston onto splined shaft stud one rotation; left hand thread (medium nose pliers / 7mm open wrench).
Note: Piston and shaft stud are left hand thread, thus screw by turning piston tool (medium nose pliers) from right to left (counter clockwise) (car front orientation).
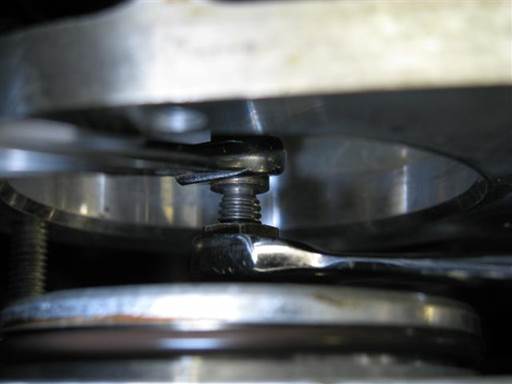
Thread exhaust piston onto splined shaft stud; left hand thread (10mm open wrench / 7mm open wrench).
Note: Piston and shaft stud are left hand thread, thus screw by turning piston tool (10mm open wrench) from right to left (counter clockwise) (car front orientation).
Moderately tighten; left hand thread (10mm open wrench / 7mm open wrench).
Note: Due to left hand thread, it is not necessary to over tighten joint.
Press vanos onto engine head until it stops.
Caution: Do not attempt to forcibly fully mount vanos to engine head. This can cause damage.
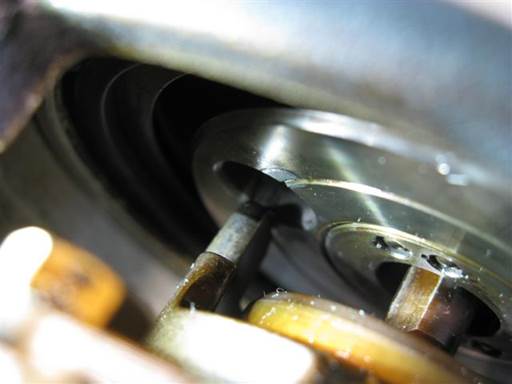
Inspect vanos oil pump side hole and intake sprocket hub side tab for alignment.
Rotate vanos oil pump as needed to achieve alignment (fingers).
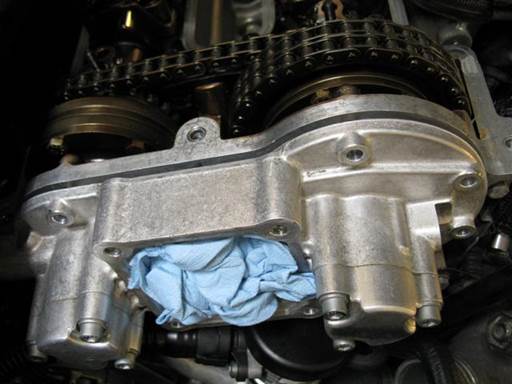
Press vanos onto engine head and verify hub tab insertion into oil pump hole.
Realign vanos pump as need to facilitate tab insertion (fingers).
Note: Vanos will not fully mate with head due to vanos sealing O-rings.
Remove vanos supporting bolts.
Repeat above procedure of mounting vanos intake and exhaust pistons to splined shafts and inserting vanos onto engine head for second bank.
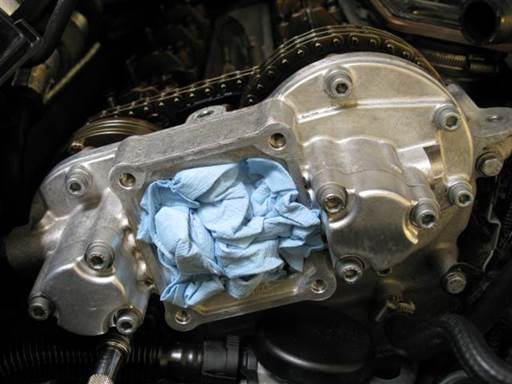
Install bank 1 & 2 vanos mounting bolts. Perform following for each vanos.
Install vanos 9 mounting bolts (5mm hex bit socket 3/8″ / 3/8″ ratchet & extension).
Tighten bolts evenly in multiple passes to draw vanos to engine head evenly.
Fully tighten, 10 Nm (7 ft-lb) (5mm hex bit socket 3/8″ / 3/8″ torque wrench & extension).
Tighten bolts evenly in multiple passes. Verify one pass with all bolts fully tightened.
Installation of vanos hydraulic attachments
Install vanos oil pressure restrictor in distribution piece (22mm open wrench).
Fully tighten (22mm open wrench).
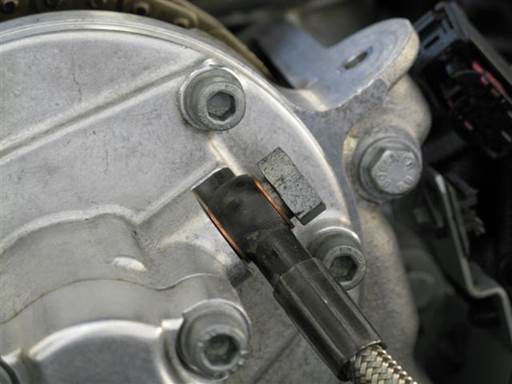
Install bank 1 & 2 vanos oil hose. For each vanos perform following.
Mount vanos oil hose on vanos. Install new crush washer on banjo bolt at each side of hose pipe fitting (picture).
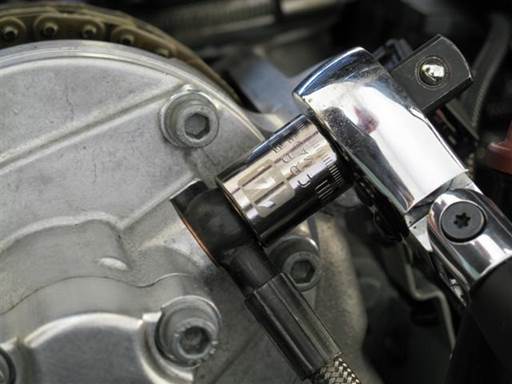
Tighten bank 1 & 2 vanos oil hose. For each vanos perform following.
Counter hold oil hose while tightening banjo bolt to keep hose form rotating (14mm socket 3/8″ / 3/8″ ratchet).
On bank 2, insert tool to interfere with hose pipe rotation (flathead).
Fully tighten, 13 Nm (9.5 ft-lb) (14mm socket 3/8″ / 3/8″ torque wrench).
Installation of vanos solenoids
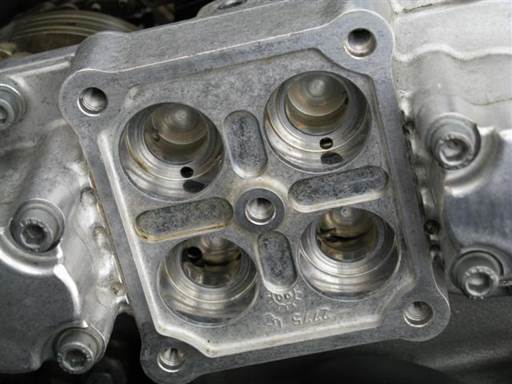
Prepare bank 1 & 2 vanos solenoid housing. For each vanos perform following.
Remove towel from vanos solenoid housing.
Inspect and clean vanos solenoid housing (brake cleaner & towels).
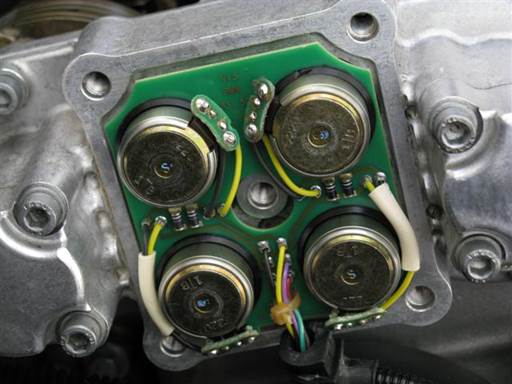
Install bank 1 & 2 vanos solenoids. For each vanos perform following.
Orient solenoids with electrical cable at bottom and insert solenoids in solenoid cavities.
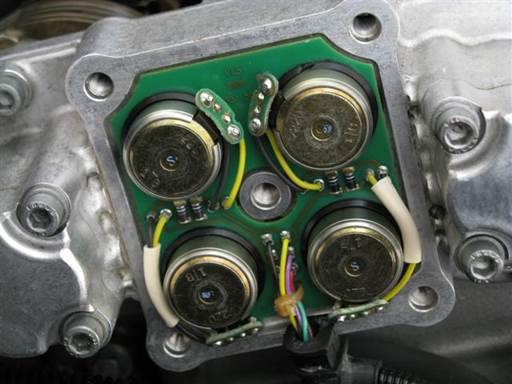
Fully insert bank 1 & 2 vanos solenoids. For each vanos perform following.
Press in on each solenoid until it inserts into solenoid cavity (thumb).
Solenoid PC board will insert into vanos housing.
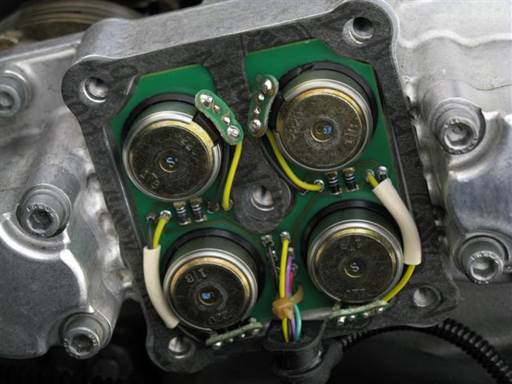
Install bank 1 & 2 vanos solenoid cover gasket. For each vanos perform following.
Insert cover gasket over solenoid electrical cable and mount gasket with middle protruding section at top (picture).
Adjust gasket middle protruding section to position under electrical wires.
Adjust electrical cable rubber boot flat end to sit against gasket (picture).
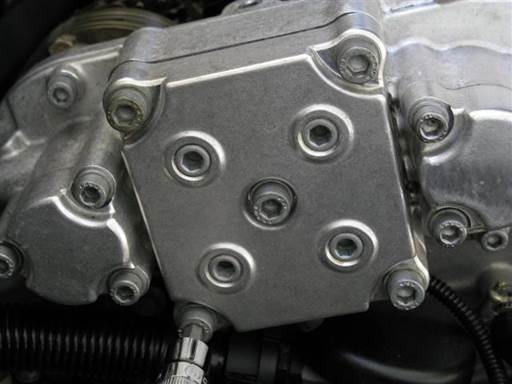
Install bank 1 & 2 vanos solenoid cover. For each vanos perform following.
Install solenoid cover on vanos with cover notch down and over electrical cable rubber boot.
Adjust cover gasket as needed to conform to vanos housing and solenoid cover.
Install cover 5 mounting bolts (hand).
Tighten cover 5 mounting bolts (6mm hex bit socket 3/8″ / 3/8″ ratchet & extension).
Fully tighten, 14 Nm (10 ft-lb) (6mm hex bit socket 3/8″ / 3/8″ torque wrench & extension).
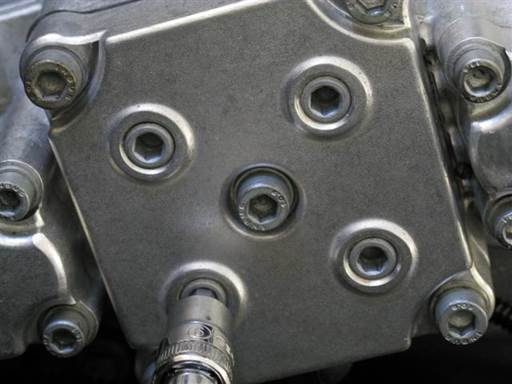
Tighten bank 1 & 2 vanos solenoid loading bolts. For each vanos perform following.
Tighten solenoid cover 4 solenoid loading bolts (6mm hex bit socket 3/8″ / 3/8″ ratchet & extension).
Fully tighten, 12 Nm (9 ft-lb) (6mm hex bit socket 3/8″ / 3/8″ torque wrench & extension).
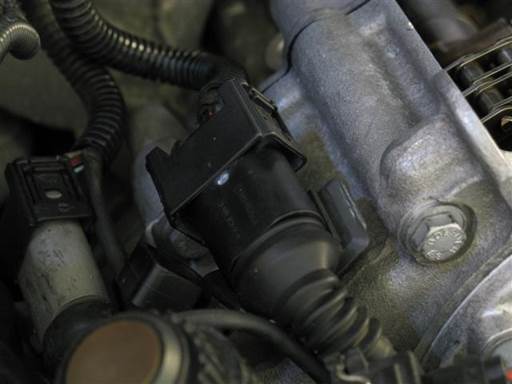
Install bank 1 & 2 solenoid electrical cable connector. Perform following for each vanos.
Route vanos solenoid electrical cable adjacent to vanos.
Connect solenoid electrical cable connector to wiring harness connector.
Press in connectors until clips snap into place.
Installation of coolant hoses
Install coolant expansion tank on thermostat housing.
Orient expansion tank into mounting position to orient hose rotational position correctly.
Press hose onto thermostat pipe.
Position hose clamp over pipe and tighten hose clamp (6mm socket 1/4″ / 1/4″ ratchet & extension).
Install coolant expansion tank cable electrical connector.
Press cable connector onto sensor until connector clip snaps into place.
Install radiator upper hose onto radiator upper neck.
Press hose connector wire clip onto hose connector before mounting hose.
Install hose connector onto radiator upper neck and align hose notch with radiator neck notch.
Press hose connector onto radiator neck until wire clip snaps into place.
Install radiator lower hose onto radiator lower neck.
Press hose connector wire clip onto hose connector before mounting hose.
Install hose connector onto radiator lower neck and align hose notch with radiator neck notch.
Press hose connector onto radiator neck until wire clip snaps into place.
Install temperature sensor electrical cable connector. Press cable connector onto sensor until connector wire clip snaps into place.
Install upper radiator hose on thermostat housing.
Press hose onto thermostat pipe.
Position hose clamp over pipe and tighten hose clamp (6mm socket 1/4″ / 1/4″ ratchet & extension).
Install lower radiator hose on thermostat housing.
Press hose onto thermostat pipe.
Position hose clamp over pipe and tighten hose clamp (6mm socket 1/4″ / 1/4″ ratchet & extension).
Installation of valve covers
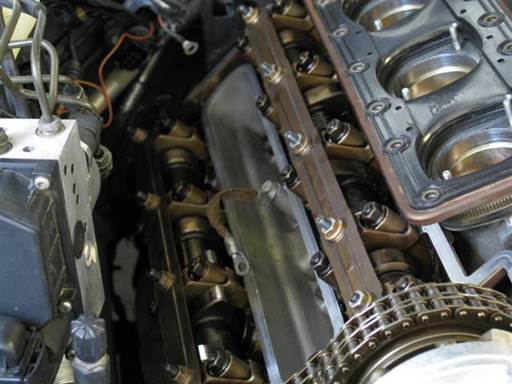
Install bank 1 & 2 camshaft oil rails. For each set of camshafts perform following.
Note: Bank 1 & 2 camshaft oil rails are different.
Note: Oil rail front is denoted by dimple between first and second hole.
Note: Intake and exhaust oil rails are same and can be switched, and oil rail top and bottom are same and can be installed either ways.
Install intake and exhaust camshaft oil rails in position over bearing cap studs.
Install 5 mounting nuts at each oil rail (10mm deep socket 3/8″ / 3/8″ ratchet, 10mm ratcheting wrench).
Fully tighten, 8 Nm (6 ft-lb) (10mm deep socket 3/8″ / 3/8″ torque wrench, 10mm ratcheting wrench).
Tighten nuts evenly. Verify one pass with all nuts fully tightened.
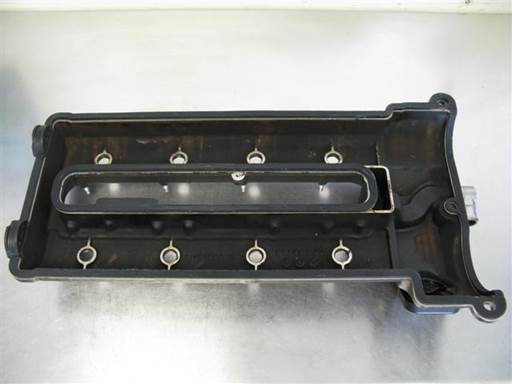
Install bank 1 & 2 valve cover gaskets. For each valve cover perform following.
Note: Bank 1 & 2 gaskets are different.
Note: Orientation of sparkplug well gasket tab is of no significance.
Align perimeter gasket with valve cover perimeter groove and sparkplug well gasket with valve cover sparkplug well groove.
Insert gaskets, ridge side, into cover grooves.
Align and fully press in gaskets into cover grooves.
Note side flaps on rear half-moon gasket section. These flaps must straddle head rear when valve cover is installed.
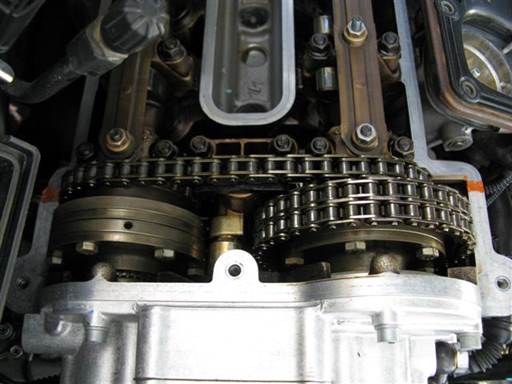
Apply bank 1 & 2 timing cover gasket sealant. For each timing cover perform following.
Place thin coat of gasket sealant at timing cover top right and left side gasket joints with head.
Allow sealant to solidify for 2 minutes before mounting valve cover.
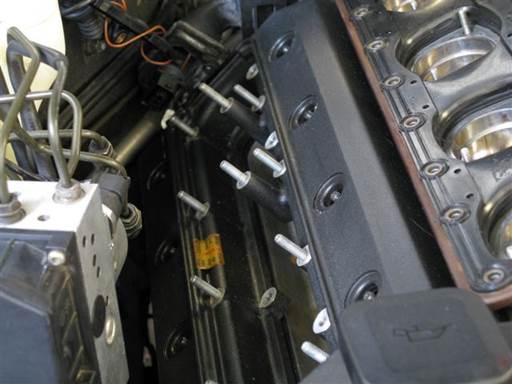
Install bank 1 & 2 valve cover. For each valve cover perform following.
Position sparkplug well ground strap in sparkplug well.
Place valve cover with gaskets on engine head.
Keep valve cover high off engine head until fully positioned at rear before lowering onto engine head. This will prevent valve cover gasket from hitting bearing cap studs and dislodging.
Adjust cover position to center cover holes with studs.
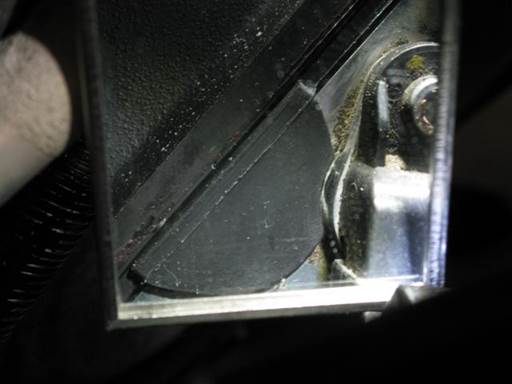
Verify bank 1 & 2 valve cover seating. For each valve cover perform following.
Inspect valve cover gasket seating along valve cover perimeter and sparkplug well (mirror & flashlight, feel).
Verify gasket 2 rear half-moons are properly inserted in head half-moons (mirror & flashlight, feel).
Half-moon rear flaps should be seated to rear of head (pictures).
Reposition cover and gaskets as needed to correctly align and seat gaskets.
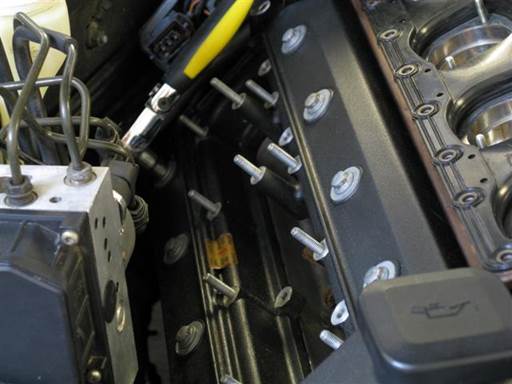
Install bank 1 & 2 valve cover mounting bolts. For each valve cover perform following.
Install 11 valve cover mounting bolts w/ washers & grommets, 3 at front and 4 at each side (10mm socket 3/8″ / 3/8″ ratchet & extension).
Note: Front 3 bolts are different than remaining 8 bolts.
Tighten bolts evenly working back and forth, assuring even pressure distribution on cover. Tighten until bolts bottom out (stop turning).
Fully tighten, 8Nm (6 ft-lb) (10mm socket 3/8″ / 3/8″ torque wrench & extension).
Install engine oil filter canister in its mounting position.
Install oil filter canister 2 mounting nuts (10mm socket 3/8″ / 3/8″ ratchet & extension).
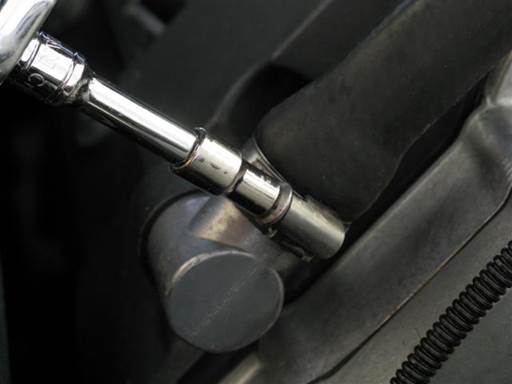
Install bank 1 & 2 crankcase ventilation hose on valve covers. For each valve cover ventilation hose perform following.
Press hose onto valve cover vent pipe.
Position hose clamp over pipe and tighten hose clamp (6mm socket 1/4″ / 1/4″ ratchet & extension).
Mount battery positive cable on bank 2 valve cover and insert into cable box.
Install battery positive cable on stud and mount with nut (19mm socket 1/2″ / 1/2″ ratchet).
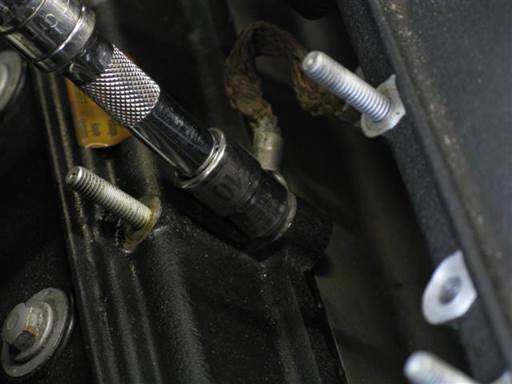
Install bank 1 & 2 valve cover ground strap. For each valve cover ground strap perform following.
Install valve cover sparkplug well ground strap with mounting bolt (10mm socket 3/8″ / 3/8″ ratchet & extension).
Note: Mounting bolt is short and should not be confuse with many intake manifold slightly longer bolts.
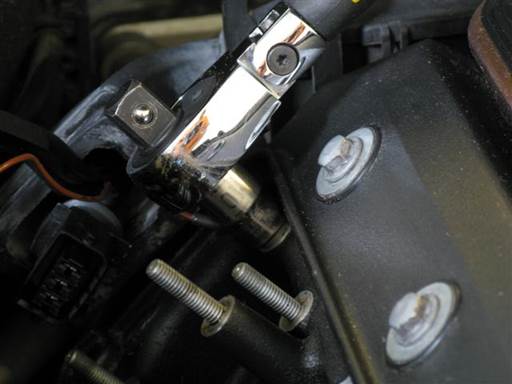
Install bank 1 & 2 coil harness ground wire at top rear of valve cover. For each coil harness perform following.
Install coil harness ground wire with mounting bolt at top rear of valve cover (10mm socket 3/8″ / 3/8″ ratchet).
Note: Mounting bolt is short and should not be confuse with many intake manifold slightly longer bolts.
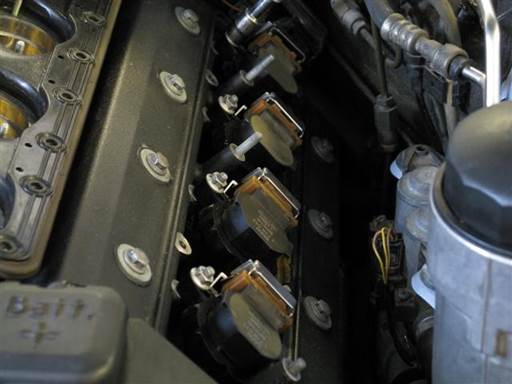
Install bank 1 & 2 ignition coils. For each bank perform following.
Install each coil into original sparkplug well and onto mounting studs and mount with 2 nuts (10mm socket 3/8″ / 3/8″ ratchet & extension).
Tighten coil mounting nuts evenly to mount coil evenly.
Note: Coil boot will not fully insert onto sparkplug during initial mount. This is normal.
Fully tighten, 9Nm (6.5 ft-lb) (10mm socket 3/8″ / 3/8″ torque wrench & extension).
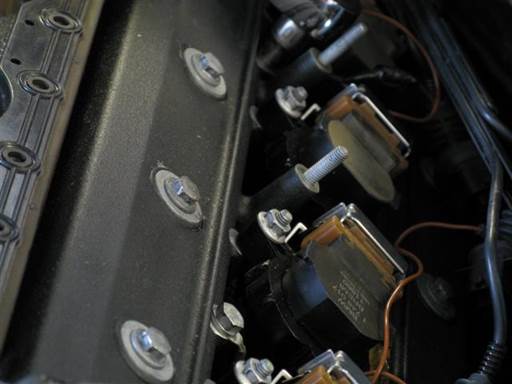
Install bank 1 & 2 coil harness ground wires on valve covers. For each coil harness perform following.
Install coil harness ground wire with mounting bolt at top middle front and rear of valve cover (10mm socket 3/8″ / 3/8″ ratchet).
Note: Mounting bolt is short and should not be confuse with many intake manifold slightly longer bolts.
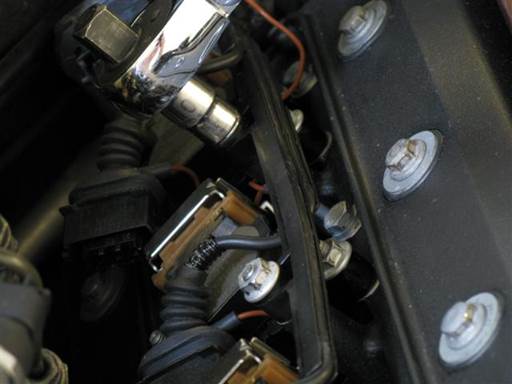
Install bank 1 & 2 coil harness rails. For each coil harness rail perform following.
Mount coil harness rail onto valve cover 2 mounting studs and install 2 mounting nuts (10mm socket 3/8″ / 3/8″ ratchet).
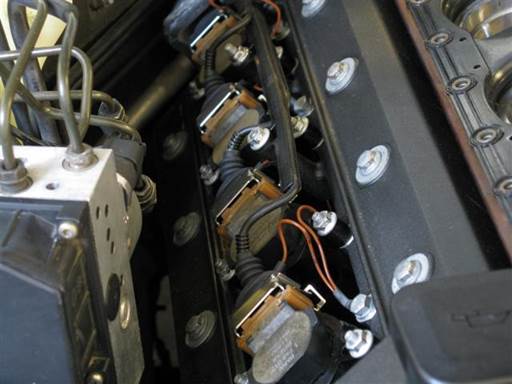
Install bank 1 & 2 ignition coils electrical cable connectors. For each set of coils perform following.
For each coil, pull up on coil connector metal lock, insert cable connector onto coil connector, and press down on coil connector metal lock.
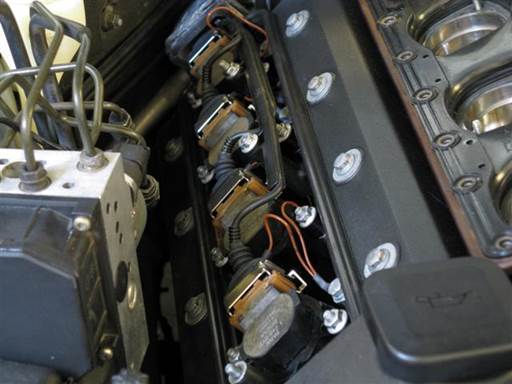
Install bank 1 & 2 coil cover gasket on valve cover. Perform following for each valve cover.
Install coil cover gasket on valve cover. Position gasket open end at rear.
Note: Bank 1 & 2 coil cover gaskets are same part.
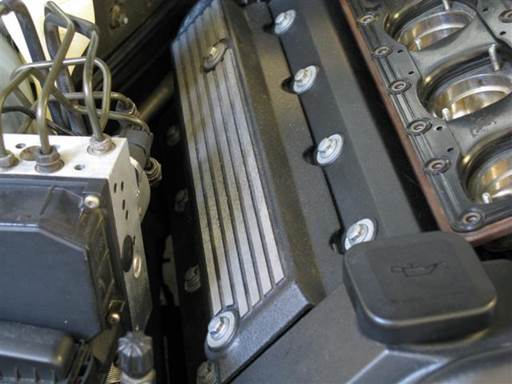
Install bank 1 & 2 coil cover on valve cover. Perform following for each valve cover.
Orient cover with end hole at front.
Align cover rear ridge to coil harness boot groove and install cover on boot and valve cover.
Install cover 2 mounting bolts w/ washers and grommets (10mm socket 3/8″ / 3/8″ ratchet).
Tighten bolts evenly working back and forth, assuring even pressure distribution on cover. Tighten until bolts bottom out (stop turning).
Install battery negative cable at battery in trunk.
Mount negative battery cable clamp on battery negative post and tighten mounting nut (10 mm socket 3/8″ / 3/8″ ratchet & extension).
Installation of intake manifold
Position components for mounting intake manifold on engine.
Route MAF sensor long electrical cobles to engine front and install in cable clip at each head.
Position idle control valve and intake manifold drain hose clamps at end of each hose with clamp bolt head at front and facing up (picture).
Position oil separators at sides of engine heads with mounting necks facing rear (picture).
Install intake manifold cover gasket on intake manifold.
Align gasket with manifold perimeter groove.
Insert gasket, ridge side, into manifold perimeter groove.
Fully press gasket into groove.
Install intake manifold cover 4 O-rings on intake manifold 4 towers.
Insert O-rings into tower O-ring grooves.
Place intake manifold on top of engine (picture).
Insert bank 1 & 2 oil separator neck grommets into intake manifold at manifold front right and left.
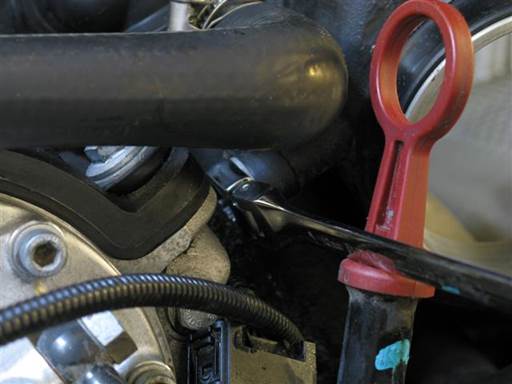
Install bank 1 & 2 oil separator mounting bolt (10mm ratcheting wrench).
Install intake manifold front lower drain hose.
Press hose onto manifold pipe.
Position hose clamp over pipe and tighten hose clamp (5mm socket 1/4″ / 1/4″ ratchet & extension).
Install intake manifold front idle control valve hose.
Press hose onto manifold pipe.
Position hose clamp over pipe and tighten hose clamp (6mm socket 1/4″ / 1/4″ ratchet & extension).
Install intake manifold mounting bolts.
Position intake manifold to align bolt mounting holes.
Install intake manifold 33 mounting bolts (10mm socket 3/8″ / 3/8″ ratchet & extension).
Tighten bolts evenly in multiple passes. Verify one pass with all bolts fully tightened.
Install air intake funnels inside intake manifold.
Mount each funnel on 2 mounting studs and fully seat.
Note: Cyl 1 & 5 are unique, and cyl 2-4 & 6-8 are same.
Install each funnel 2 mounting nuts (10mm socket 3/8″ / 3/8″ ratchet & extension).
Tighten nuts evenly in multiple passes.
Install intake manifold cover on intake manifold.
Install intake manifold cover 15 mounting caps; 4 top and 11 perimeter (10mm socket 3/8″ / 3/8″ ratchet & extension).
Tighten caps evenly in multiple passes. Verify one pass with all caps fully tightened.
Installation of cabin filter housing
E39 cabin filter housing installation
Installation of fan & shroud
Installation of engine air intake
Engine air intake installation
Post repair procedures
Mix 2 gallons of coolant. BMW coolant is mixed 50/50% coolant/distilled water.
Remove coolant expansion tank cap.
Pour coolant into expansion tank until coolant level reaches max line on tank side.
Start engine.
Pour coolant into expansion tank until coolant level reaches max line on tank side.
Install expansion tank cap.
Drive car until coolant and engine fully warmed up.
Unscrew expansion tank cap until air leaks out.
Close expansion tank cap.
Check coolant level and fill as needed when engine is fully cold (morning).
© 2024 Beisan Systems LLC