E39 Thrust Arm Bushing Write-up
The following information is provided for reference purposes only and should be used at your own risk
In no event shall Beisan Systems, LLC or its members be liable for incidental, consequential, or special loss or damages of any kind however caused.
Introduction
One of the most wearable components of the E39 front suspension system is the thrust arm bushing. Its lifespan is approximately 60k “20k miles. The bushing is a fluid filled rubber cylinder wrapped in a metal sleeve. It sits inside the thrust arm bore and acts as a shock absorber. Over time and wear, the rubber tears and the fluid leaks out. This leaves behind a distinctive diagnostic indicator which presents as a spill mark on the bottom exterior of the bushing sleeve and thrust arm bore. The bushing needs to be replaced, although consideration should be given to replacing the complete thrust arm.
The following is a discussion on the thrust arm bushing failure symptoms and diagnosis, and an E39 R&R (remove and replace) procedure.
Symptoms
Intermittent steering wheel shimmy (side to side shaking) at a certain speed interval, usually 50-60 MPH. The shimmy can occur only when braking or only when not braking. The symptoms sometimes heighten in the morning before the tires warm up. Symptom nuance characteristics can also change if the suspension configuration is modified; Examples: tire pressure, tires, wheel balance, wheels, brakes, rotors, etc. Thus owners can be misled into perceiving the problem is resolved due to symptom changes caused by suspension adjustments.
Symptoms other than steering wheel shimmy can also occur:
- Front tire inner tread wear and cupping.
- Intermittent front end clunk on stops and/or starts.
- ABS engagement during moderately heavy braking on rough pavement.
- Less responsive handling.
- Less responsive braking.
Unfortunately, the symptoms can be shared with other faulty suspension related components, like out of round rotors. Thus a proper diagnosis is important to identifying the failure.
Configuration Background
Before discussing diagnoses, it’s helpful to have some understanding of the front suspension arm configuration.
There are two front suspension arms, and they both incorporate a bushing. They are the Thrust Arm, and the Control Arm. BMW calls the thrust arm, Tension Strut on the E39 6-cylinder, and Traction Strut on the E39 8-cylinder. The common name is Thrust Arm.
The front suspension arms are found at each front wheel. They both connect between the wheel carrier (ball joint) and the frame (bushing joint). They form a “triangle” between the wheel carrier and the frame. This triangle provides good symmetry for lateral and longitudinal suspension balance. The thrust arm is longer than the control arm. It takes on a steeper angle and rises higher to the frame, and thus is also called an Upper Control Arm. It handles much of the longitudinal (fore/aft) car jarring, and consequently takes on much abuse and wear. The control arm is shorter. It takes a smaller angle and rises less to the frame than the thrust arm, and thus is also called a Lower Control Arm. It handles much of the latitudinal (side to side) movement, and consequently takes on less load forces and lasts longer than the thrust arm.
On the 6-cyl (picture, left front), the thrust arm mounts on top of the wheel carrier shelf and heads to the front (picture right), and thus is also called a Leading Control Arm. The control arm mounts on bottom of the wheel carrier shelf and heads to the rear (picture left), and thus is also called a Trailing Control Arm.
On the 8-cyl, the two arms switch directions, and thus the thrust arm is a Trailing Control Arm and the control arm is a Leading Control Arm. They are both mounted on bottom of the wheel carrier shelf.
The bushing end of the thrust arm has a cylindrical bore that holds a bushing. The bushing is a rubber cylinder with an outer metal sleeve and an inner metal shaft. In recent BMW builds (E39 included), the bushing rubber is filled with hydraulic fluid. The bushing mounts inside the thrust arm bore and is held in place by pressure. The bushing outer diameter is slightly larger (~.3mm) than the thrust arm bore diameter, so once in position, the pressure of metal against metal holds it in place. The center shaft allows for a bolt to run through the bushing and mount the thrust arm to the frame. The bushing acts as a shock absorber during wheel movements.
Over time and wear the bushing rubber ends tear, allowing the inner fluid to leak out, and causing the bushing to fail.
The control arm bushing has a similar structure to the thrust arm bushing. It differs in that it’s built into the arm (one component), is fully rubber (not fluid filled), and is smaller in size. Like the thrust arm, it also acts as a shock absorber during wheel movements.
Over time and wear the bushing rubber dries, hardens, and then tears. This causes the bushing to fail.
The ball joint ends of both arms are the same. The arm end has a socket built in, and the mounting bolt morphs into a ball at the arm end. The ball diameter is larger than the socket rim diameter and thus the ball is permanently recessed into the socket. The ball fits snugly into the socket, leaving no room for “play”. The joint is greased and encapsulated in a protective rubber boot. The ball joint allows joint rotation during wheel movements, while maintaining a tight connection between the arm and the wheel carrier.
The ball joint ball and socket matting surfaces deteriorate/shrink with use and wear and a space in the joint slowly develops. This space creates “play” in the suspension configuration thus changing its designed characteristics. The ball joint rubber boot can also tear, allowing the grease to leak out. This will cause friction in the ball joint and significantly increase joint wear. The rubber boot is not available separately and the ball joint will likely have encountered excessive wear, thus its replacement is not viable.
The third arm connected to the wheel carrier is the Outer Tie-rod Arm and is a component of the steering system. It has a ball joint at the wheel carrier and incorporates a horizontally positioned ball joint as part of the arm at the steering end. On the 6-cyl it mounts at the front bottom of the wheel carrier shelf. On the 8-cyl it mount at the rear bottom of the wheel carrier shelf.
The ball joints deteriorate and fail in the same manner as the suspension arm ball joints.
Diagnosis
A thrust arm bushing fails when a section of its rubber tears and its internal fluid leaks out. A failure diagnosis is attained by noting the rubber tear or the fluid leak.
A bushing rubber tear can be inspected by prying (~18″ pry bar) each bushing end away from the frame and looking for the tear. It is unfortunately difficult to get a clear view of the rubber ends while the bushing is mounted. Another approach is to disconnect the bushing from the frame. This will facilitate a clear view and inspection of the bushing rubber ends, but unfortunately the removal and remount of the bushing is somewhat involved. Some components need to be removed to allow room for removing the bushing bolt, and the car needs to be in “normal position” to perform the final mount tightening. The specifics of these procedures are covered in the repair section (below).
A rubber tear can in some cases be at the sleeve side and not be visibly discernable. In such cases a fluid leak indication is necessary for denoting the failure.
Inspecting for a fluid spill is an easier diagnosis approach than looking for a rubber tear. When the fluid leaks out it leaves a fluid spill mark on the bottom exterior of the bushing sleeve and arm bore.
The 6-cyl has two cutouts in the engine compartment shield (under front of car) that allow for thrust arm bushing inspection. BMW engineers must have felt this was a wearable part and needed frequent inspection. The fluid spill mark can be easily seen through the cutout.
Taking off the engine compartment shield (Philips screwdriver) and then the plastic single side cover (10mm socket/driver) over the bushing joint, allows for a fuller inspection. With the protection covers off the distinctive spill mark can be easily denoted.
On the 8-cyl, the thrust arm is a trailing arm (rear of front of car) and the bushing joint is exposed. This is a small determent to the diagnosis, since dirt can accumulate on the joint making the spill mark less obvious. Noting the spill mark on the bushing sleeve and the overall spill outline helps to clarify the image.
If the bushing rubber tear is at the sleeve edge the fluid leak can be very slow and not cause a spill mark indication. In such cases noting a small active leak at a bushing end bottom is necessary for denoting the failure. Prying (~18 pry bar) the bushing at the sleeve might cause some remaining fluid to leak out.
Unfortunately in some cases a rubber tear, spill mark, or leak can not be denoted. In such cases the symptoms and the bushing lifespan might need to be depended on for the assessment.
Note: Checking the wheels and thrust arm for play does not produce an indication of thrust arm bushing failure. Prying (pry bar) at the bushing also does not produce a failure indication, as new and failed bushings can have seemingly equivalent movements.
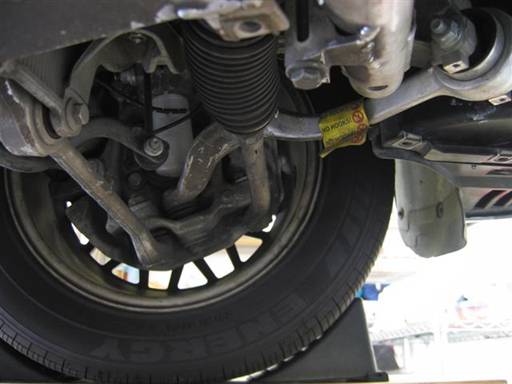
The thrust arm bushing can be replaced, but if the thrust arm ball joint is worn then both thrust arm and bushing should be replaced. Thus it’s important to assess the state of the thrust arm ball joint before proceeding with a repair.
It is most effective to look for play in the thrust arm ball joint when the joint is disconnected from the wheel carrier. The bolt (ball) can be pushed in/out of the arm (socket) repetitively to detect any play (free space). Unfortunately dismounting the ball joint from the wheel carrier requires disconnecting the strut at the wheel carrier and a special tool to remove the ball joint bolt from the wheel carrier shelf.
The ball joint can be assessed while mounted but this takes some finesse and experience. The arm (socket) is pushed/pried on/off the bolt (ball) to look for play. A ~18″ “pry bar” is an ideal tool for this task. On the 6-cyl, wedge the pry bar between the strut butt and ball joint head, to press the socket towards the ball, and between the wheel carrier shelf and the arm stem adjacent to the rubber boot, to expand the socket away from the ball. On the 8-cyl, utilize the shelf and arm stem for the expansion, and the wheel inner rim and ball joint head for the press. Play is denoted by a slight swift movement in response to a small amount of applied pressure. Smooth incremental movement due to increasing/decreasing pressure is due to ball joint rotation and does not denote free space.
A worn thrust arm ball joint causes a symptom of click/clunk sound on sudden suspension movement, such as car starts and stops.
The control arm bushing is also diagnosed by utilizing a ~18″ pry bar. Markedly push the control arm end laterally to one side and then the other. Leverage the pry bar between the arm end and the frame at the bushing. Look for rubber tears. Also look for rubber resilience (spring); the arm end should bounce back when released.
A failed control arm bushing will produce similar symptoms to a failed thrust arm bushing.
The control arm ball joint is diagnosed in the same manner and has the same symptoms as the thrust arm ball joint.
The outer tie-rod wheel carrier ball joint can also be diagnosed in the same manner as the thrust arm and control arm ball joints.
An overall system ball joint inspection can be performed by wheel manipulation. Play in any of the aforementioned ball joints can be engaged by maneuvering the wheel. The car front wheels will need to be off the ground to perform this inspection. Place one hand on the tire 12 o’clock inner shoulder, and the other hand on the wheel rim 6 o’clock outer lip. Engage your shoulder at the 12 o’clock end. Attempt to push in at the 6 o’clock position. Look for a quick small movement. This will indicate play (free space). Reposition hands and shoulder to leverage the wheel in the opposite direction.” Place one hand on the tire 6 o’clock inner shoulder, and the other hand on the wheel rim 12 o’clock outer lip. Engage your shoulder at the 6 o’clock end. Attempt to push in at the 12 o’clock position. Again, look for a quick small movement which will indicate play. Any play in either test direction indicates ball joint wear at the ball joints mounted on the wheel carrier shelf. Individual ball joint inspection is necessary to isolate the faulty ball joint(s).
Perform the same inspections as above but rotate the wheel from side to side, 3 & 9 o’clock. There will be an initial movement until the steering lock limit is reached. Otherwise the test is the same as above. Any play in these directions indicates outer tie-rod inner ball joint wear.
A technique similar to the wheel manipulation scheme can be applied during an alignment procedure. The steering wheel can be turned to one side, and then the other. Any non proportional change in toe or camber numbers is an indication of a worn ball joint(s).
A thrust arm bushing could be expected to last approximately 60k “20k miles. A thrust arm ball joint could be expected to last the lifespan of two or three thrust arm bushings. A control arm could be expected to last the lifespan of two thrust arms (ball joint). These are very rough estimates, and individual experiences will vary significantly. Suspension wear is greatly influenced by road conditions and suspension balance. An out of round/balance tire/wheel can significantly increase wear on bushings and ball joints.
Repair Considerations
The solution to a torn thrust arm bushing is to replace the bushing. The thrust arm bushing is an independent part and can be replaced separately. If the thrust arm ball joint is worn then the thrust arm needs to be replaced, as the ball joint is an integral part of the arm.
The following is a study of several thrust arm bushing repair approaches. These discussions will also implicitly address approaches to replacing the thrust arm (ball joint).
“
BMW calls for replacing the thrust arm bushings in pairs. The bushings are sold in pairs.
BMW Technique
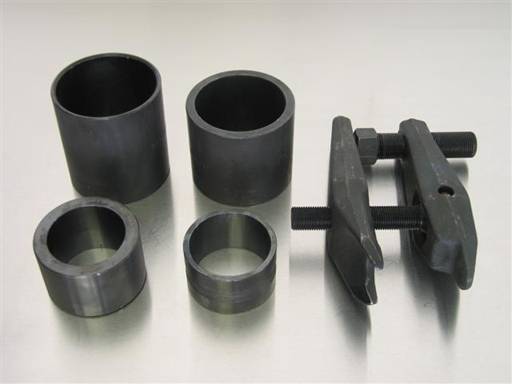
BMW’s approach to replacing the thrust arm bushing is to, disconnect the thrust arm from the car, utilize a hydraulic press to press out the old bushing and press in the new bushing, and then remount the arm. The bushing joint is mounted to the frame with a bolt and nut and can be disconnected with standard tools. The 6-cyl needs the brake air duct removed, and the 8-cyl needs the stabilizer bar mounts disconnected, to facilitate access and removal of the bushing mounting bolt. The ball joint bolt expands in a conical shape at its base and thus causes the forming of a tight bond between the bolt and wheel carrier shelf when mounted. A BMW special tool, part # 99-88-6-31-2-240 (picture right), is needed to dislodge the bolt from the wheel carrier shelf. To remove the ball joint the strut (shock) needs to be loosened from the wheel carrier bearing and the wheel carrier lowered on the strut to facilitate needed space. To slide the wheel carrier down on the strut the wheel carrier bearing needs to be lubricated and expanded at the seam with a lever bar (large flathead). The wheel carrier bearing seam needs to be aligned to a strut mark when remounting. The mark is either found on a strut label (R & L), or is drawn on the strut before dismounting.
To press out/in the bushing from the thrust arm BMW has designed a set of press/receive sleeves (cylinders) to facilitate the press (picture, 6-cyl right, 8-cyl left). 6-cyl, part# 99-88-6-31-2-270, $22.63 (includes 271 & 272); 8-cyl part# 99-88-6-31-2-260, $37 (includes 261 & 263).
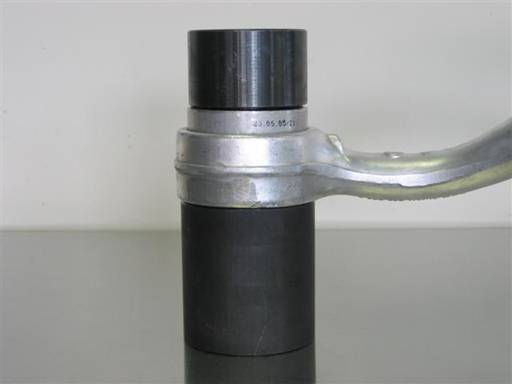
A receive (lower) sleeve supports the thrust arm bore on its perimeter while facilitating room for a full bushing to recess into the sleeve. A press (upper) sleeve sits on the bushing metal sleeve inner rim and is pressed by the hydraulic press to insert the bushing through the thrust arm bore. The old bushing is pressed through completely, while the new bushing is pressed in to a center position in the arm bore.
Reinstalling the arm involves the extra wrinkle of tightening the bushing/frame bolt/nut while the car is in “normal position”. This requires the car to be resting on its wheels on a level surface with a full tank of gas and weighed down with 500 lb in a specific configuration. Fortunately this can be achieved more practically by manipulating the suspension into the needed position.
The biggest complication of the BMW technique for a DIY job is the need for the hydraulic press. Although a hydraulic press can be acquired in an inexpensive ($150+) simple implementation (bottle jack and metal frame housing), its size and infrequent use make it impractical for the average DIYer. A local BMW dealership or indy shop could be hired to perform the press, but the logistics of accomplishing this in the middle of the repair are difficult and precarious. In addition to the hydraulic press obstacle, there”s also the added complexity of removing the ball joint so the arm can be taken to the hydraulic press. There”s also the cost of the BMW special tools.
Complete Arm Replacement Technique
One often touted approach is to replace the complete thrust arm instead of just the bushing. This is usually combined with purchasing after market arms that have preinstalled bushings. New BMW OEM thrust arms do not have preinstalled bushings. OEM bushings are acquired separately and need to be installed. A BMW dealership or indy shop could be hired to perform the installation. The complete arm replacement approach alleviates the logistics of having the bushings pressed in/out by a mechanic during the repair process. The low cost of after market arms with preinstalled bushings lowers the cost overhead of replacing the complete arm.
At Car Bushing Repair Technique
If the repair is to only replace the bushings, then BMW’s technique can be greatly simplified by avoiding two of its fundamental approaches. First, to not disconnect the ball joint since it’s not directly related to the problem. Second, to not utilize a hydraulic press, but to employ a smaller mobile press tool to perform the press at the car while the ball joint is still mounted.
This is not a unique approach. BMW utilizes this method on the E39 rear end bushing repairs. “The BMW tool sets for these cases employ a spindle (bolt) that runs through the bushing center shaft and facilitates a press cup and nut and receive cup to press in/out the bushing. This technique might not have been utilized by BMW on the thrust arm bushing due to the bushings large size and proportionally narrow center shaft; i.e. too much force on a small spindle.
There are after market tool manufacturers that have produced tools to perform “at car” bushing presses. Below are two such tools for the thrust arm bushing.
SIR Tools, Bushing Master Kit, part# BMW3021, $200, is a kit that addresses the various BMW model front control/track (thrust) arm bushings. Unfortunately the kit has not been updated to include the E39.
Technic Tool Supply, Trailing Arm Set, part# BMW38-39 + Zinko 8 ton hydraulic hand pump, $285 + $375, is a kit that specifically addresses the E39 & E38 thrust arm bushings. The E38 and E39 8-cyl utilize the same thrust arm bushing. Unfortunately, the tool’s astronomical price makes it nonviable.
Jaw Puller & Pipe Cap Press Technique
An at car thrust arm bushing press can be accomplished by utilizing a 3 arm jaw puller (gear puller), a heavy duty short pipe cap, and the BMW thrust arm bushing press sleeve (referenced above).
The jaw puller jaw teeth grasp the back perimeter of the thrust arm bore, while the jaw puller bolt pushes on the pipe cap which sits on the bushing metal sleeve. Tightening the bolt causes the pipe cap to press the bushing through the thrust arm bore.
The BMW press sleeve is inserted between the pipe cap and bushing and is pressed through the thrust arm bore to drive out the end portion of the bushing remaining in the arm bore.
Thrust Arm, Bushing, Sleeve | 6-cyl | 8-cyl |
Bushing length | 60 | 63 |
Bushing diameter | 58.3 | 66.4 |
Bushing shaft length | 68 | 76 |
Bushing shaft end stud length | 4 | 6.5 |
Press sleeve length | 35 | 40.6 |
Press sleeve diameter (outer) | 57.7 | 65.5 |
Arm bore diameter (inner) | 58 | 65.9 |
Arm bore length | 31 | 38.8 |
Arm bore perimeter thickness | 8 | 6 |
Measurements in mm
1 1/2″ Socket Weld Pipe Cap | 3k psi | 6k psi |
Press cap diameter (outer) | 65 | 69.8 |
Press cap diameter (inner) | 49 | 49 |
Press cap length (outer) | 32.7 | 38.7 |
Press cap length (inner) | 14.7 | 14.7 |
Measurements in mm
There are several tool (puller & pipe cap) parameters that need to be taken into consideration.
The puller needs to be strong enough to handle the press forces; have fine bolt threads to facilitate hand/wrench tightening; long enough to accommodate the longest apparatus, new bushing initial insertion; and the jaw teeth short enough to not protrude into the bore bushing path, although a longer tooth length can also be worked with.
A 5 1/2″ (6″) 5 ton 2/3 jaw puller (7mm jaw teeth) generally accommodates these specifications, although the length is at the limits of the longest 8-cyl apparatus.
The pipe cap needs to be wider than the bushing outer diameter to fully seat on the bushing sleeve; not wider than the arm bore outer diameter so as not to touch the puller jaws; deep enough to avoid the bushing shaft end stud; short enough to facilitate the longest apparatus; strong enough to handle the press forces.
A 1 1/2″ forged steel socket weld pipe cap accommodates these specifications. The 3k psi version works well for the 6-cyl parameters, but a wider 6k psi version is needed to accommodate the 8-cyl larger diameter bushing.
Repair Procedure
The following is an E39 thrust arm bushings R&R (remove and replace) procedure.
A wheel alignment should be performed after the repair.
Repair time ~5 hours.
Parts, Tools, and Shop Supplies
Thrust Arm (tension strut) Bushing Set (31-12-9-068-753) $85/each
2 x Thrust Arm Bushing Self-Locking Nut (33-32-6-751-446) $0.82/each
8-cyl:
Thrust Arm (traction strut) Bushing Set (31-12-0-006-482) $37/each
2 x Thrust Arm Bushing Self-Locking Nut (31-12-1-092-110) $0.60/each
Jaw (gear) Puller: 2/3 jaw, 5 1/2″ (6″), 5 ton (7mm jaw teeth):
– Powerbuilt, part # 648909, $35, Pepboys Auto
– Performance Tool, part # W87127LT, loaner, Pepboys Auto
– OEM, part # 25919, $40, Autozone
– OEM, part # 27078, loaner, Autozone
Press cap, 1 1/2″ forged steel socket weld pipe cap, 6-cyl 3k psi $5, 8-cyl 6k psi, $10, industrial pluming supply. Note: need smooth cap top center, no raised writing.
Press sleeve, BMW (pressure sleeve), 6-cyl 90-88-6-312-272 $9.45/each, 8-cyl 90-88-6-312-263 $18/each; if can’t be acquired then need to purchase tool set, 6-cyl 90-88-6-312-270, 8-cyl 90-88-6-312-260
1/2″ combo wrench
1/2″ socket 3/8″, 5/8″ socket 1/2″
3/8″ ratchet, 1/2″ ratchet
8-cyl:
Press cap, 2″ common 150 psi pipe cap, hardware store
Note: Needed for initial insertion of bushing since 1 1/2″ 6k psi pipe cap too tall for 6″ puller. A longer puller (> 6″) alleviates the need for this part. The 2″ 150 psi pipe cap can not be utilized for the complete press process since it will likely collapse.
Optional:
12″ metal pipe 3/4″; to extend ratchet length for press process
Compressor; to replace ratchet for press process
18mm combo wrench
8mm socket 1/4″, 10mm socket 1/4″, 18mm socket 1/2″
1/4″ ratchet driver, 1/2″ ratchet (listed above), 1/2″ (or 3/8″ w/ 1/2″ converter) torque wrench (110 Nm [81 ft-lb])
8-cyl:
21mm instead of 18mm, 1/2″ torque wrench (127 Nm) [94 ft-lb])
13mm socket 1/2″ instead of 8&10mm sockets and driver
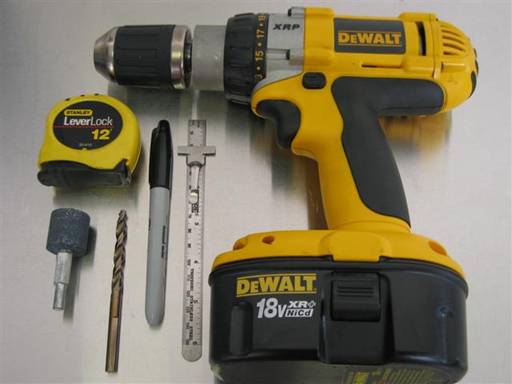
Drill, 1/4″ steel drill bit, grind drill bit, metric ruler (Empire, Northern Tools or Sears), magic marker, tape measure
8-cyl:
Not shown: 8 1/2″ x 11″ paper, paper tape
Paper towels, brake cleaner, fine grade (~220) sandpaper, 6 ft rope, graphite based grease (Sta-Lube, Synthetic Grease, CRC)
2 x 3 ton jack stands, jack w/ wood blocks as needed for height increase
Reference end of repair for application
500lb of weight in 150, 150, 150, 50 lb unit sizes
Example: 10 x 50lb sand bags
Reference preparation below for application
Preparation
Thoroughly clean bushing sleeve (brake cleaner / towel).
Locate arrow marking on bushing rubber end. Either end will do. Mark edge of sleeve at arrow point (magic marker).
Mark a 14.5mm (8-cyl 12.5mm) point down side of sleeve from arrow point (magic marker).
Repeat procedure for second bushing.
8-cyl:
Arrow marking found only on one bushing end.
8-cyl:
Draw a circumference line around bushing sleeve, at opposite end from previous alignment mark, ~5mm from bushing sleeve end edge.
Wrap paper end around bushing sleeve (8 1/2″ end of paper). Overlap and align paper ends, tighten wrap, and tape paper at overlap (paper tape). Adjust paper edge position to be ~5mm down from bushing end edge. Draw a circumference line around bushing sleeve at paper edge (magic marker). Roll bushing on a table top while holding marker steady from above to facilitate drawing a clean line.
Repeat procedure for second bushing.
Note: The 8-cyl bushing initial insertion is difficult as the bushing easily tilts and misaligns. The circumference line will be useful for making alignment adjustments to facilitate a true alignment insertion.
Utilize grinder (drill & grind drill bit) to remove any raised writing on pipe cap top center.
Utilize drill and drill bit (1/4″) to create a ~4mm dimple in center of pipe cap(s). Indentation should be large enough to fully receive jaw puller bolt tip and allow for slight side to side movement. A little grease is recommended for this type of drilling.
Clean jaw puller bolt threads and apply graphite based grease, brushing into threads. Thread bolt through yoke to remove excess grease.
To tighten the thrust arm bushing bolt/nut at the end of the repair, BMW requires the car be in “normal position”.
This method is utilized for most front end suspension repairs, and is necessary to assure the bushing center is locked with the frame (tightened) at a neutral / middle of range suspension position. As the suspension maneuvers (up/down), the bushing outer sleeve will rotate/torque, but the center shaft will be locked in with an independent frame. The middle rubber bushing will consequently be twisted/torqued. To attempt to minimize this stress, the bushing center is tightened down in a suspension neutral / middle of range position, “normal position”.
“Normal position” requires the car to be resting on all four wheels (level ground), with tires properly inflated (info at driver door frame), a full gas tank, and the car weighed down with 500lb; specifically: 150lb in each front seat (seat in center position), 150lb in center of back seat, 50lb in center of trunk. Note: The car needs to be moved some after weighing down to allow the suspension to settle into the intended position.
Tightening the thrust arm bolt/nut with the car on the ground is quite difficult. As an alternative, “normal position” can be emulated by jacking up the wheel carrier to the position achieved by the configuration. Of course to accomplish this, the position of the wheel carrier in that configuration, “normal position”, would need to be known in advance.
Fill car gas tank. Inflate tires to proper pressures. Load car with 150lb in each front seat (seat in center position), 150lb in center of back seat, 50lb in center of trunk. Move car to settle suspension. Park car on level ground. Note: This is quite important to achieving a proper reading.
Remove front wheels center caps. Measure distance between wheel hub center cup bottom lip and fender rim directly above. Verify second front wheel has exact reading. If not, then car may not be on level ground.
This measurement technique can be replicated when the wheel is off the car, which is the practical setup when performing the repair.
Note: On my car, 528i 2000 5sp standard suspension touring 225/55 R16, the measurement decreased by 1/2″ between the configuration without the weights (17 1/2″) and then with the weights (17″).
Repair
Raise front of car and place on jack stands (follow appropriate procedure; chock both sides of both rear wheels). Remove front wheels. Remove large engine compartment shield underneath front of car.
The following procedure shows the left side (driver side). The right side is the same but with minor noted differences.
It’s more effective to perform the left side first since it’s illustrated with pictures.
8-cyl:
Insert and turn car key in ignition to unlock steering wheel.
Remove stabilizer (sway) bar fame mounts (13mm socket 1/2″ / 1/2″ ratchet).
No need to remove liners in the next several steps. Go directly to disconnecting thrust arm bushing joint.
Remove thrust arm bushing joint plastic cover (10mm socket 1/4″ / 1/4″ driver).
Note: right and left bushing joint covers are unique.
Remove 5 screws from wheel well lower front splash guard (8mm socket 1/4″ / 1/4″ driver).
Remove 2 screws from brake air duct in wheel well (8mm socket 1/4″ / 1/4″ driver).
Right side: Unclip temperature sensor on bottom of wheel well splash guard and push into access hole. Take note of mounting position for end reinstallation.
Unfasten splash guard and air duct connection. Remove splash guard.
Note: splash guard bottom sits inside bumper, and top fits behind upper splash guard.
Remove last screw of brake air duct found inside bumper (8mm socket 1/4″ / 1/4″ driver). Remove brake air duct, taking note of mounting position for end reinstallation.
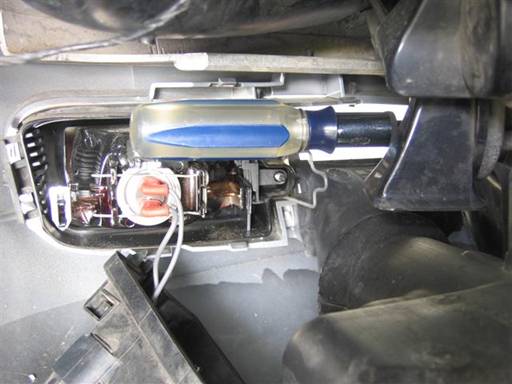
Left side: Brake air duct screw inside the bumper is difficult to access. Unclip and remove fog light rear cover. Only a direct socket extension access is feasible.
Break thrust arm bushing nut seize (18mm combo wrench) (8-cyl 21mm). Note: No space for socket tool.
8-cyl: Turn wheel fully to outside to facilitate access to bolt head.
Counter hold thrust arm nut and unscrew bolt (18mm combo wrench, 18mm socket 1/2″ / 1/2″ ratchet) (8-cyl 21mm). Remove bolt by adjusting thrust arm (forward) to allow bolt to slip out. Allow thrust arm to drop and wrest on tie rod (arm).
8-cyl: After nut is removed, move steering back near to the center. Bolt will scarcely clear center link at tie rod ball joint. A center link bend at that location provides the needed clearance. The steering will need to be moved slightly while bolt is being removed. Steering is moved from under car by pushing on steering system.
This is a good opportunity to check the thrust arm ball joint. Rotate the arm (socket) on the bolt (ball). Movement should be stiff. Push arm (socket) in/out of bolt (ball). There should be no play (space). Check rubber boot for tears and grease leakage.
Any ball joint play or torn boot and the thrust arm needs to be replaced. Replace both thrust arm bushings.
Tightly strap thrust arm to tie rod to keep it from moving (cross tie with rope; tie to arm, then utilize 2 half-hitch knots on each cross, strongly tightening each half-hitch).
Note: A very tight strapping is necessary to minimizes thrust arm movements during press process.
8-cyl: Thrust arm ties on bottom side of tie rod.
Thoroughly clean bushing insertion side (car inboard side) metal sleeve and thrust arm bore exterior (brake cleaner / towel, sandpaper).
Note: Cleaning bore exterior will also facilitate detection of next bushing tear (spill mark).
Note: When utilizing brake cleaner at car, spray cleaner on towel and then clean with towel. This method safeguards from inadvertently spraying brake cleaner on car rubber parts which can detrimentally affect them.
Bring parts and tools needed for bushing extraction and insertion to working area underneath car (new bushing, puller, press cap, press sleeve, grease, metric ruler, 1/2″ combo wrench, 1/2″ socket 3/8″, 5/8″ socket 1/2″, 3/8″ ratchet, 1/2″ ratchet).
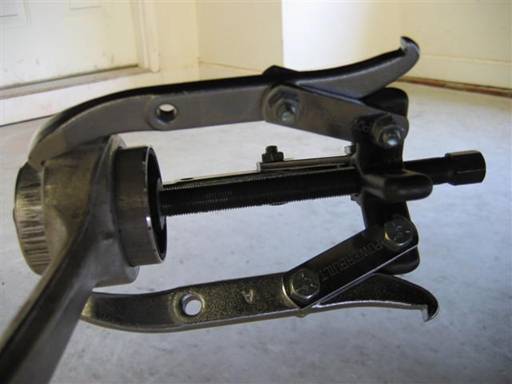
1st side: Loosen small nuts on puller links enough to allow for movement of jaws and yoke (1/2″ combo wrench, 1/2″ socket 3/8″ / 3/8″ ratchet).
Thread/unthread puller bolt to insert ~80mm into puller yoke. Orient puller so main body is on bore insertion side (car inboard side), and jaw teeth are on the bore extraction side (car outboard side). Straddle thrust arm bore with puller jaws/teeth. Insert puller bolt into bushing center shaft. Hold jaw arms around bore with one hand while tightening puller bolt with other. Bolt thread is wider than bushing shaft and will stop bolt, thus creating needed back pressure on yoke. Moderately tighten puller bolt so puller is fully suspended from thrust arm (5/8″ socket 1/2″ / 1/2″ ratchet).
8-cyl: If puller bolt thread width narrower than bushing shaft, insert press cap and center on bushing sleeve, as performed in next step.
2nd side: Strongly tighten loosened link nut/bolt (1/2″ box wrench, 1/2″ socket 3/8″ / 3/8″ ratchet).
1st side: Adjust jaws to be evenly distributed around bore. Adjust jaw teeth to be completely inserted and perpendicular to bore. Jar jaw ends to adjust teeth (ratchet handle butt).
Tighten puller links bolts/nuts (1/2″ box wrench, 1/2″ socket 3/8″ / 3/8″ ratchet). Adjust puller jaws and teeth as before, but with more precision. Strongly tighten puller bolt. Strongly tighten links bolts/nuts.
8-cyl: Puller jaw teeth are deeper than arm bore perimeter width and thus will not insert fully.
Loosen puller bolt and unthread ~40mm from bushing. Puller jaws will loosen, but puller will continue to be suspended from thrust arm.
Place some grease on press cap center area. Insert press cap into puller bolt path. Push press cap against bolt, inserting puller bolt tip into press cap dimple. Tighten puller bolt until press cap mates with bushing sleeve. Center press cap on bushing sleeve. **Check and adjust puller jaw teeth.
While grasping puller with one hand for leverage and stability, tighten puller bolt (5/8″ socket 1/2″ / 1/2″ ratchet). After a few turns, a “crack” might be heard, indicating breaking of bushing seize. Continue “press” until press cap reaches and mates with thrust arm (puller bolt will tighten).
Note: Lubricants and grease on bushing sleeve provide no benefit to press process.
Unscrew puller bolt ~40mm. Insert press sleeve between press cap and bushing. Push press sleeve against press cap, and press cap against puller bolt. Tighten puller bolt until press sleeve mates with bushing sleeve. Center press cap on press sleeve, and press sleeve on bushing sleeve. Tighten puller bolt (5/8″ socket 1/2″ / 1/2″ ratchet). Finely adjust press sleeve by taping it (ratchet handle butt). Press sleeve will be precisely positioned when bushing sleeve can be seen from around whole outside perimeter of press sleeve. **This is essential, and will take some effort to achieve. **Check and adjust puller jaw teeth.
Note: Thrust arm bore is notched at rim to facilitate small deviation adjustments of press sleeve during initial insertion.
While grasping puller with one hand for leverage and stability, tighten puller bolt (5/8″ socket 1/2″ / 1/2″ ratchet). A crack or two might be heard initially, indicating adjustment of press sleeve by bore rim notch. Continue tightening until bushing slips out of bore (will feel lessening of pressure).
8-cyl: Do not press bushing completely out of arm bore. Press until ~10mm of press sleeve remains outside bore, allowing ~8mm of bushing to remain in arm bore. This facilitates remounting puller with new bushing while old bushing is present to keep puller jaw teeth from protruding into arm bore opening.
Loosen puller bolt and remove press cap. Remove puller by allowing yoke to drop down towards floor and then slipping out jaw teeth from bore. Take care not to alter jaw positions. Remove press sleeve from the bore.
Note: Picture shows press sleeve inside arm bore.
8-cyl: Puller does not come off arm due to the remaining bushing. Loosen one jaw link bolt/nut at yoke (1/2″ box wrench, 1/2″ socket 3/8″ / 3/8″ ratchet). This allows jaw to expand out and puller to slip off bushing / thrust arm.” Take care not to alter any other jaw positions.
Thoroughly clean bore interior (brake cleaner / towel).
Note: Make sure new bushing sleeve and arm bore are clean, dry, and have no grease.
Unwind puller bolt fully to allow room for new bushing and press cap. Place some grease on press cap center area. Place back puller in reverse of removal. Insert press cap into puller bolt path, and push against puller bolt. Orient bushing so bushing end with marks is at press cap and marks lines up with orientation ridge on thrust arm (bore rim at arm neck). Insert new bushing in puller bolt / press cap path, and push against press cap. Tighten puller bolt, allowing bushing to enter thrust arm bore. Again, orient bushing so marks on sleeve lines up with orientation ridge on thrust arm. Center press cap on bushing sleeve. Tighten puller bolt (5/8″ socket 1/2″ / 1/2″ ratchet). **Check and adjust puller jaw teeth. It’s essential they don’t protrude into bore opening.
8-cyl:
Utilize 2″ (150 psi) pipe cap for initial insertion of bushing (~10mm), then loosen puller bolt and replace with 1 1/2″ (6k psi) pipe cap.
Strongly tighten loosened link nut/bolt (1/2″ box wrench, 1/2″ socket 3/8″ / 3/8″ ratchet) after initial bushing, press cap, and puller setup.
Once initial alignment setup is complete, begin to slowly tighten puller bolt in 1/4 turn increments. Adjust any slight bushing tilt by tapping on bushing sleeve at press cap (ratchet handle butt). Utilize drawn circumference line as an alignment reference. Repeat incremental insertion and adjustment process until bushing is inserted sufficiently (~5mm) to assure insertion alignment. Loosen puller bolt and realign as needed.
While grasping puller with one hand for leverage and stability, tighten puller bolt (5/8″ socket 1/2″ / 1/2″ ratchet). When sleeve balance mark approaches bore edge, start measuring both ends of bushing sleeve (metric ruler). Stop press when both bushing ends protrude 14.5mm (8-cyl 12.5mm) from bore (equally protrude).
8-cyl: Old bushing will be pressed out by new bushing.
Loosen puller bolt and remove press cap. Allow puller yoke to drop down towards floor. Loosen one jaw link bolt/nut at yoke (1/2″ box wrench, 1/2″ socket 3/8″ / 3/8″ ratchet). This allows jaw to expand out and puller to slip off bushing / thrust arm.” Take care not to alter any other jaw positions (useful for the second side).
Clean bushing bolt and washer, and car fame mounting perimeters (brake cleaner / towel). Untie rope holding thrust arm to tie rod. Bring thrust arm back up to frame mount position. Align bushing shaft with frame bolt holes by moving thrust arm up/down and forward/backward. Look through frame hole to check alignment. Note bolt washer alignment ridges mate with bolt head. Insert bolt into frame/bushing from brake air duct side (8-cyl car inboard side). Adjust bushing position as needed (forward) to allow bolt through. Thread new self-locking nut onto bolt. Counter hold nut and tighten bolt (18mm box wrench, 18mm socket 1/2″ / 1/2″ ratchet) (8-cyl 21mm). Tighten bolt until snug, then loosen 1/2 turn. Align bolt washer ridges to bolt head.
Repeat above procedure for second side. Clean and re-grease puller bolt. Puller should be reused with little adjustment to jaws. Bushing press flow goes from car inboard side to car outboard side. It’s the mirror image of the 1st side setup.
Adjust car front lift height to be as low as safely possible (3 ton jack stands on lowest setting) (use appropriate procedure).
For each side: Utilize lift (jack) to raise front wheel carrier to its “normal position”. Measure distance between wheel hub center cup bottom lip and fender rim directly above, as performed in initial height assessment. Align bolt washer ridges to bolt head. Fully tighten bushing bolt/nut to 110 Nm (81 ft-lb) (18mm box wrench, 18mm socket 1/2″ / torque wrench) (8-cyl 21mm 127 NM (94 ft-lb)).
Lower wheel carrier.
Note: Caution should be utilized during this step as the weight of the car is supported on the suspension.
Note: To achieve wheel carrier “normal position” height, car will likely lift from jack stand (picture). Draw outline of jack stand perimeter on floor before raising wheel carrier. This facilitates returning jack stand to its original position incase of movement. After raising wheel carrier, raise jack stand height to provide closer backup support. Return jack stand to original height before lowering wheel carrier. Minimizing car front height will reduce car lift from jack stand (3 ton jack stands on lowest setting).
Note: Point wheel direction strait forward. Lock steering wheel and remove keys from ignition. This locks wheel carrier directional movement. Apply lift (jack) to wheel carrier perpendicularly from car outside (picture). This minimizes potential hub rotation, or side loading and slippage.
Note: Optimal placement of lift at wheel carrier is unclear. Leverage at wheel hub (picture) could exert excessive force and damage wheel bearings. Wheel hub can also rotate. Leverage under wheel carrier shelf could exert excessive force and damage ball joint(s). Utilize wood block to facilitate access of lift to wheel carrier shelf.
8-cyl: Reinstall stabilizer (sway) bar fame mounts (13mm socket 1/2″ / 1/2″ ratchet).
For each side:
8-cyl: Skip this section.
Insert brake air duct into position and install 1 screw in bumper (8mm socket 1/4″ / 1/4″ driver).
Insert wheel well splash guard. Bottom inserts inside bumper. Top inserts behind upper splash guard.
Right side: Bring through temperature sensor, and mount into position.
From underneath car, reconnect wheel well splash guard and brake air duct. Separate first, then reinsert.
Install 5 screws for wheel well splash guard, and 2 screws for brake air duct (8mm socket 1/4″ / 1/4″ driver).
Install thrust arm bushing plastic cover with 2 bolts (10mm socket 1/4″ / 1/4″ driver). Right and left covers a unique. Clip top part of cover on first then install bolts.
Install large engine compartment shield underneath front of car.
Remount front wheels and lower car (follow appropriate procedure).
A wheel alignment should be performed after the repair.
To my mom, may she always be blessed.
Rajaie (Palestinian)
© 2024 Beisan Systems LLC