E39 Swing Arm Ball Joints Write-up
The following information is provided for reference purposes only and should be used at your own risk
In no event shall Beisan Systems, LLC or its members be liable for incidental, consequential, or special loss or damages of any kind however caused.
Introduction
One of the most wearable components of the rear suspension system is the swing arm ball joint. Its lifespan is approximately 75k “20k miles.
The following is a short discussion on the swing arm ball joint failure symptoms and diagnosis, and an E39 (non T) R&R (remove and replace) procedure.
Symptoms
- Rear swerve/tramline during turns/slaloms.
- Rear vibration/shimmy.
- Rear squeaks, often heard over bumps and when entering and exiting car.
- Rear tire inner tread wear and cupping.
Configuration Background
The swing arm ball joint takes on a much different form than the rest of the ball joints found at the end of suspension arms on the E39. The swing arm ball joint is an independent component/part. It consists of a center metal shaft/pipe and a metal cylindrical sleeve which encircles the shaft outside at the approximate shaft center. At the mating point of the two parts, the shaft outside morphs into a ball, and the sleeve inside morphs into a socket, and thus the ball joint designation. The ball joint is packed in grease, and the matting ends are sealed with rubber boots which are mounted with metal O-rings.
The ball joint is mounted on the inside of a bore at the bottom rear of the rear wheel carrier. The integral link (a shaft like component) connects at the front end of the ball joint shaft. The swing arm outboard ends encompass and mate with the ball joint and integral link ends. A long bolt runs through (left to right, picture) the swing arm, ball joint / wheel carrier, integral link, and again swing arm, mounting them all together.
The ball joint allows a tight connection between the wheel carrier and swing arm, while not inhibiting the vertical movements of the wheel carrier.
The ball joint ball and socket matting surfaces deteriorate/shrink with use and wear and a space in the joint slowly develops. This space creates “play” in the suspension configuration thus changing its designed characteristics.
The ball joint rubber boots can also tear, allowing the grease to leak out. This will cause friction in the ball joint and significantly increase joint wear. The rubber boot is not available separately and the ball joint will likely have encountered excessive wear. Thus the resolution is to replace the ball joint.
Diagnosis
Raise rear of car and place on jack stands (use appropriate procedure; chock both sides of both front wheels). Release emergency brake and place transmission in neutral.
For each rear wheel perform the following.
Position yourself on your knees at the wheel. Place one hand on the tire 12 o’clock inner shoulder, and the other hand on the wheel rim 6 o’clock outer lip. Engage your shoulder at the 12 o’clock end. Attempt to push in at the 6 o’clock position.
Note: That’s my pastor friend from Syria, 70 years old. Loves working on the car!
Look for play in the wheel movement. This will be a small but quick movement, free space. A small incremental movement proportional to incremental pressure is normal.
Note: The ball joint is packed in grease and sometimes that can inhibit the “free space” movement, making the diagnosis difficult. The next step is more definitive.
If you find play, have a second person perform the above diagnosis procedure while you inspect the ball joint on the wheel inboard side. The ball joint is the metal/rubber component that’s located at the bottom rear of the wheel carrier. If you see one of the rubber boots move, that’s an indication of free space in the ball joint and thus a faulty joint.
Inspect the ball joints rubber boots for any indication of rubber tear and/or grease leak. If any tear or leak is found, the ball joint needs to be replaced.
Repair Procedure
The following is an E39 (non T) swing arm ball joints R&R (remove and replace) procedure.
A wheel alignment should be performed after the repair.
Repair time ~6 hours.
Parts, Tools, and Shop Supplies
2 x Ball Joint (33-32-1-095-631) $33.92/each, 2 x Snap Ring (33-32-1-091-687) $1.26/each, 2 x Self locking nut (33-32-1-092-385) $5.00/each, 2 x stabilizer bar link self-locking nut (at swing arm) (33-32-1-092-382) $1.60/each (not shown)
Ball Joint Press (90-88-6-334-190) $74.25, Spindle (90-88-6-333-333) $71.00
8mm combo wrench, 5/8″ [~16mm] combo wrench (≤ 9″), 16mm combo wrench (≤ 9″), 18mm combo wrench
8 mm socket 1/4″, 10mm socket 1/4″, 13mm socket 3/8″, 18mm socket 1/2″, 24mm (~15/16″) socket 1/2″, 24mm (~15/16″) deep socket 1/2″
1/4″ ratchet, 3/8″ ratchet w/ extension, 1/2″ ratchet, 1/2″ torque wrench (105 Nm [77 ft-lb], 256 Nm [189 ft-lb]) (Craftsman, etc.), 1/2″ breaker bar (24″)
Measuring tape, needle nose pliers, small chisel, large flathead screwdriver, ~1lb dead blow hammer, claw hammer (common), 18″ pry bar
Paper towels, brake cleaner, spray lubricant, graphite based grease (Sta-Lube, Synthetic Grease, CRC)
Wire brush (stainless steel only), 3″ 2×4 wood block, medium grade sanding paper and sanding block
Not shown: Jack and pad towel.
Preparation
To tighten the integral link bolt (105 Nm) and swing arm bolt/nut (256 Nm) at the end of the repair, BMW requires the car be in “empty weight position” or “normal position” (i.e. “normal position” optional).
This method is utilized for most rear end suspension repairs, and is necessary to assure the bushing center is locked with the frame (tightened) at a neutral / middle of range suspension position. As the suspension maneuvers (up/down), the bushing outer sleeve will rotate/torque, but the center shaft will be locked in with an independent frame. The middle rubber bushing will consequently be twisted/torqued. To attempt to minimize this stress, the bushing center is tightened down in a suspension neutral / middle of range position, “empty weight position” or “normal position”.
“Empty weight position” requires the car to be resting on all four wheels (level ground), with tires properly inflated, and a full gas tank.
“Normal position” requires, in addition to “empty weight position” requirements, that the car be weighed down; specifically: 150lb in each front seat (seat in center position), 150lb in center of back seat, 50lb in center of trunk.
Tightening the integral link bolt and swing arm bolt/nut with the car on the ground is quite difficult. As an alternative, “empty weight position” or “normal position” can be emulated by jacking up the wheel carrier to the position achieved by the configuration. Of course to accomplish this, the position of the wheel carrier in that configuration, “empty weight position” or “normal position”, would need to be known in advance.
Fill car gas tank. Inflate tires to proper pressures. For “normal position”, load car with 150lb in each front seat (seat in center position), 150lb in center of back seat, 50lb in center of trunk; move car to settle suspension. Park car on level ground. Note: This is quite important to achieving a proper reading.
Remove rear wheels center caps. Measure distance between wheel hub center cup bottom lip and fender rim directly above. Verify second rear wheel has exact reading. If not, then car may not be on level ground.
This measurement technique can be replicated when the wheel is off the car, which is the practical setup when performing the repair.
Note: On my car, 528i 2000 5sp standard suspension touring 225/55 R16, the measurement decreased by 1″ between the configuration without the weights (16 1/2″) and then with the weights (15 1/2″).
Repair
Raise rear of car and place on jack stands (follow appropriate procedure; chock both sides of both front wheels). Remove rear wheels. Keep parking brake engaged.
The following procedure shows the left side (driver side). The right side is the same but with minor noted differences.
It’s more effective to perform the left side first since it’s illustrated with pictures.
As needed in the following two link removal steps, utilize a lift (jack) to raise the wheel carrier, easing applied force on link and facilitating bolt removal.
Right side: xenon lights: Disconnect level sensor regulating rod joint. Counter hold inside nut and remove outside nut (needle nose pliers, 10mm socket 1/4″ / 1/4″ ratchet). Remove bolt, and rotate regulating rod down.
Check regulating rod ball joints as described below for stabilizer bar link.
Disconnect stabilizer bar link joint at swing arm. First, push aside ball joint boot from inside nut (flathead). Counter hold inside nut and remove outside nut (5/8″ [~16mm] combo wrench, 16mm combo wrench). If tool not fitting well on inside nut, then repeat boot removal attempt. Inside nut has only two flat facets, so outside nut might need to be turned to spin inside nut into a tool accessible orientation.
Remove stabilizer link bolt and rotate link away from swing arm. Pull down on stabilizer bar link, or push down on stabilizer bar to facilitate bolt removal.
This is a good opportunity to check the stabilizer bar link ball joints. Twist bolt / link on both ends to rotate ball / socket joints. Movement should be stiff. Push/pull each bolt (ball) in/out of link (socket) to look for play (free space). There should be no movement. Check link rubber boots for tears.
Any ball joint play (free space) or rubber tear and link needs to be replaced (easy to perform at a later time).
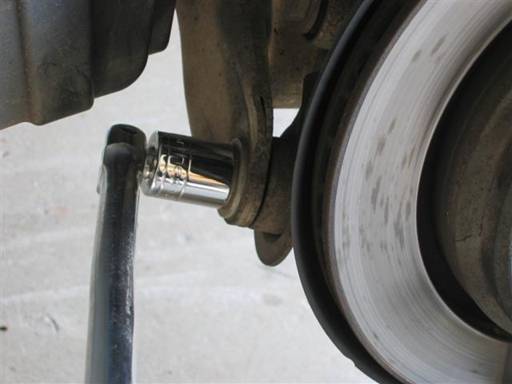
Remove swing arm mounting nut. Break nut seize (24mm socket 1/2″ / 1/2″ breaker bar), then counter hold bolt and remove nut (18mm combo wrench, 24mm socket 1/2″ / 1/2″ ratchet).
Withdraw swing arm mounting bolt from swing arm front end (car front). Nudge bolt tip back (dead blow hammer), or if resistant unscrew from bolt head. Unscrew at bolt head for final removal from swing arm front end. Bolt tip will now be in integral link, and integral link will have drop down.
Leverage (pry bar) against axel to press down swing arm front end, and simultaneously pull out mounting bolt. Bolt tip will stop at ball joint.
Unscrew bolt out of ball joint to completely remove (hand).
Note: Axel can be pulled towards wheel carrier to prevent CV boot contact with tool.
Remove integral link bolt (18mm socket 1/2″ / 1/2″ breaker bar & 1/2″ ratchet). Remove integral link from swing arm.
Leverage (pry bar) against axel to push down swing arm, and pull up and out” on rotor bottom to detach swing arm and wheel carrier at ball joint.
Leverage (pry bar) against axel to press down on swing arm, and wedge a separator (wood block) between axel and swing arm at inboard end of swing arm.
Lift rotor up and push forward (car front) to further separate wheel carrier from swing arm.
Remove snap ring from ball joint rear end (hammer / chisel, needle-nose pliers).
Note: The first owner of my car (00-03) lived in Connecticut, so the ball joint parts were quite oxidized and rusted. The snap rings were essentially welded to the wheel carrier.
Clean dirt/rust on ball joint front and rear end outer sleeves and wheel carrier bore rim (brake cleaner/towel, sand paper/block). Apply lubricant to bore rim (spray lubricant).
Note: This step minimizes the forces applied on the press tool spindle (bolt) and is essential to the proper function and maintenance of the spindle.
Note: When utilizing brake cleaner at car, spray cleaner on towel and then clean with towel. This method safeguards from inadvertently spraying brake cleaner on car rubber parts which can detrimentally affect them.
Apply grease to press tool spindle (bolt) fine threads (especially at spindle end section) (graphite based grease). Also apply grease to press tool nut bottom and receive plate center, where nut contacts.
Note: This step is essential to the proper function and maintenance of the tool.
Twist press tool small press cap onto ball joint rear end so that it’s flush with metal sleeve.
Arrange spindle with receive sleeve (notched cylinder) and plate (notched puck), and orient receive sleeve/plate notch to align with wheel carrier protrusion. Insert spindle from receive plate through ball joint shaft and thread into press cap on other end (8mm combo wrench). Spindle end should protrude from press cap end, but not be tightened to press cap. Thread to end then loosen 1/2 turn.
Tighten press nut until press cap and receive sleeve are flush with ball joint metal sleeve ends (24mm deep socket 1/2″ / 1/2″ ratchet). Double check all seating and alignment.
Tighten press nut until ball joint is completely removed from wheel carrier bore (press tool will loosen) (24mm deep socket 1/2″ / 1/2″ ratchet).
Remove press nut tightening tool (ratchet, then deep socket), and pull press tool out of wheel carrier bore. Loosen press nut (24mm deep socket 1/2″ / 1/2″ ratchet), and unscrew spindle from press cap (8mm combo wrench). Twist off press cap from ball joint.
Clean wheel carrier bore inside and rims (brake cleaner/towel, sand paper/block).
Note: Wheel carrier bore and new ball joint should be clean and free of grease/lubricant.
Twist large press cap onto new ball joint front end (wider sleeve) so that it’s flush with metal sleeve. Insert ball joint rear end into wheel carrier bore/rim front.
Arrange spindle with receive sleeve and plate, and align receive sleeve and plate notch to match swing arm protrusion. Insert spindle from receive plate through ball joint shaft, and thread into press cap on other end (8mm combo wrench). Spindle end should protrude from press cap end, but not be tightened to press cap. Thread to end then loosen 1/2 turn.
Tighten press nut until press cap and receive sleeve are flush with ball joint metal sleeve ends (24mm deep socket 1/2″ / 1/2″ ratchet). Double check all seating and alignment.
Tighten press nut until ball joint is completely inserted and pressed against wheel carrier (press nut will get tight) (24mm deep socket 1/2″ / 1/2″ ratchet).
Loosen press nut (24mm deep socket 1/2″ / 1/2″ ratchet), and unscrew spindle from press cap (8mm combo wrench). Twist off press cap from ball joint.
Note: Once repair is completed, be sure to clean grease from press tool for good maintenance.
Install (fingers) new snap ring onto ball joint rear end sleeve. Orient ring opening to bottom.
Note: Snap ring not shown in picture (see second picture below).
Clean swing arm and integral link mounting contact surfaces and bolt threads and washers (brake cleaner/towel, stainless steel brush).
Leverage (pry bar) against rear axel to push down swing arm, and remove separator wedge.
Insert integral link long shaft end onto ball joint front end external shaft.
Align integral link to wheel carrier and mount with integral link bolt (18mm socket 1/2″ / 1/2″ ratchet). Tighten until snug, then loosen 1/2 turn.
Lift rotor up and push forward (car front) to allow ball joint rear to position closer to swing arm mounting position.
Pry (pry bar) between swing arm and wheel carrier to position ball joint end inside swing arm.
Push down swing arm (pry bar) and push in on rotor bottom (hand), so rotor lower end inserts as far inwards as possible.
Force swing arm up into ball joint mounting position (dead blow hammer).
Utilize rod (flathead) to finely align swing arm and ball joint mounting positions.
Insert mounting bolt into swing arm and thread into ball joint.
Leverage (pry bar) against axel to press down swing arm front end, and simultaneously push bolt through to swing arm front end.
Leverage (pry bar) against axel to press down on swing arm front end and press out on integral link to align their mounting positions. Simultaneously, thread in mounting bolt.
Thread bolt until fully inserted (18mm socket 1/2″ / 1/2″ ratchet).
Thread on new self-locking nut. Counter hold bolt and tighten nut (18mm combo wrench, 24mm socket 1/2″ / 1/2″ ratchet). Tighten until snug, then loosen nut 1/2 turn.
Lift wheel carrier to position of “empty weight position” or “normal position” as previously measured (tape measure). Utilize lift (jack and towel) to lift up on swing arm at its lowest point; found adjacent to wheel carrier inboard side at ball joint.
Note: If utilizing “normal position”, car will likely lift off jack stand (picture).
Tighten integral link bolt to 105 Nm (77 ft-lb) (18mm socket 1/2″ / 1/2″ torque wrench).
Counter hold swing arm bolt and tighten self-locking nut to 256 Nm (189 ft-lb) (18mm combo wrench, 24mm socket 1/2″ / 1/2″ torque wrench).
Lower wheel carrier.
Clean stabilizer bar link swing arm mounting contact surfaces and bolt thread and washer (brake cleaner/towel).
Mount stabilizer bar link joint at swing arm (16mm combo wrench, 5/8″ [~16mm] combo wrench). Adjust link ball joints and push down on stabilizer bar as needed to insert link bolt.
Note: Washer installs on outside with self-locking nut. Orient washer side with grooves to nut.
Right side: xenon lights: Clean regulating rod level sensor mounting contact surfaces and bolt thread and washer (brake cleaner/towel). Mount level sensor regulating rod (10mm socket 1/4″ / 1/4″ ratchet, needle nose pliers).
Repeat procedure for second side.
Remount rear wheels and lower car (use appropriate procedure).
Start car and pump brake pedal several times to tighten brake caliper pitons.
This is very important!!
A wheel alignment should be performed after the repair.
To my mom, may she always be blessed.
Rajaie (Palestinian)
© 2024 Beisan Systems LLC